ALL >> Business >> View Article
Choosing The Right Fittings For Your Project: Forged Fittings Vs. Welded Fittings
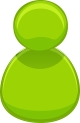
In the realm of piping systems, selecting the appropriate fittings is vital to ensure the success and longevity of any project. Two popular options, forged fittings and welded fittings, each have their own advantages and disadvantages. In this blog post, we'll delve into the pros and cons of both types so that you can make an informed decision based on your project requirements.
Forged Fittings:
Forged fittings play a crucial role in piping systems that require superior performance in high-pressure and critical applications. These metal components are created through a rigorous manufacturing process that involves shaping heated material under extreme pressure. The end result is fittings with exceptional strength, durability, and resistance to fatigue. Let's explore the advantages and disadvantages of using forged fittings:
Pros of Forged Fittings:
Strength and Durability: Forged fittings are renowned for their exceptional strength and durability. They possess the ability to withstand high-pressure applications, making them ideal for critical ...
... systems.
Resistance to Fatigue: The forging process aligns the grain structure of the material, providing enhanced resistance against fatigue and stress corrosion cracking.
Uniformity and Consistency: With precision production techniques, forged fittings maintain uniformity and consistency in dimensions. This ensures a tight and secure fit within piping systems.
Cons of Forged Fittings:
Cost: The manufacturing process for forged fittings involves intricate steps, which can result in higher production costs compared to welded fittings.
Limited Size Range: Typically, forged fittings are available in a limited size range. This might pose challenges for projects requiring larger or non-standard dimensions.
Welded Fittings:
Welded fittings play a crucial role in piping systems. They are made by joining two or more metal pieces through welding. This involves melting and fusing the materials together to create a strong and long-lasting connection. The beauty of welded fittings lies in their ability to be cost-effective and versatile in terms of sizing, making them suitable for a wide range of applications. This process offers its own set of advantages and disadvantages:
Pros of Welded Fittings:
Cost-Effective Production: Welded fittings generally offer a more cost-effective production method, making them an attractive option for projects with budget constraints.
Versatility in Sizes: Welded fittings come in a wide range of sizes, making them suitable for various applications, including those requiring large or custom dimensions.
Ease of Installation: Installing welded fittings is relatively straightforward, and the welding process allows for customization on-site, facilitating adaptability to specific project needs.
Cons of Welded Fittings:
Reduced Strength: Compared to forged fittings, welded fittings may have lower strength, especially in critical applications where high pressure and temperature are involved.
Potential for Defects: The welding process introduces the possibility of defects such as porosity and incomplete fusion, which can compromise the integrity of the fitting.
Conclusion:
Choosing between forged fittings and welded fittings ultimately depends on the specific requirements of your project. For applications where strength, durability, and resistance to fatigue are paramount, forged fittings are the preferred choice. On the other hand, if cost-effectiveness, versatility in sizing, and ease of installation are key considerations, welded fittings may be more suitable.
When it comes to reliable and high-quality fittings, Nexus Alloys and Steel stands out as a leading manufacturer. With state-of-the-art manufacturing facilities and top-grade materials at our disposal, Nexus Alloys and Steel ensures that their forged and welded fittings meet the highest industry standards. Consider opting for Nexus Alloys and Steel for your project; rest assured that you are investing in fittings that prioritize both performance and durability.
Add Comment
Business Articles
1. Now Is The Time To Apply For A $1000 Same Day Payday LoansAuthor: Lucy Lloyd
2. Short Term Loans Online: A Vital Source Of Capital
Author: Robert Miller
3. The Benefits Of Acoustic Fencing For Residential And Commercial Properties
Author: Vikram kumar
4. Iso/iec 27001 Vs Iso/iec 27701: What Is The Difference Between Data And Privacy Security?
Author: Sqccertification
5. Why Local Seo Is The Lifeline For Small Businesses This Year
Author: Alpesa Media
6. The Power Of Authentic Vedic Rituals At Trimbakeshwar
Author: Shree Trimbakeshwar
7. Eicher 242 Tractor – A Small Tractor With Big Power For Indian Farmers
Author: KhetiGaadi
8. Top 10 Jewelry Editing Mistakes To Avoid For Perfect Shots
Author: ukclippingpath
9. Luxury Vacation Rentals In Nashville Tn
Author: Marcos Skyler
10. Top Booking Mistakes Hosts Should Avoid In Cabin Rentals
Author: Top Booking Mistakes Hosts Should Avoid in Cabin
11. The Importance Of Driveways In Multistory Building: Functionality, Safety, And Aesthetic Appeal Of A Building
Author: Vikram kumar
12. Rust Prevention Additives: The Amelioration Of Metal Protection Across All Industries
Author: Ivar
13. What Are Corrosion Inhibitors And Why Are Needed To Protect Metal Life?
Author: Ivar
14. Threaded, Socket Weld, Or Butt Weld? Choosing The Right Connection For Your Pipeline
Author: Online fittings
15. Mandatory Documents Required For Iso 45001 Certification
Author: Jenny