ALL >> Automobiles >> View Article
Overview Of Disc Brake Rotors
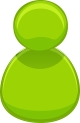
Disc Brake Rotor:
Disc Brake Rotor is commonly made up of cast iron, but in some cases it may be made of composites like, reinforced carbon–carbon or ceramic matrix composites. This is connected to the wheel and/or the axle. To stop the wheel, friction material in the form of brake pads, mounted on a brake caliper, is forced mechanically, pneumatically, hydraulically or electromagnetically against both sides of the disc.
History :
The development and use of Disc brake rotor is began in England in the 1890s. The first caliper-type automobile disc brake rotor was patented by Frederick William Lanchester in his Birmingham, UK factory in 1902 and utilized successfully on Lanchester cars.
Function:
A disc brake rotor is a wheel brake that slows rotation of the wheel by the friction caused by pushing brake pads against a brake disc with a set of calipers. Friction causes the disc and attached wheel to slow or stop. When compared with drum brakes, disc brakes offer better stopping performance, since the disc is more readily cooled. As a result disc brakes are less prone to brake fade, and recovers ...
... quickly from immersion (wet brakes are less effective).
Unlike the drum brakes, disc brake has no self-servo effect and its braking force is directely proportional to the pressure applied on the brake pad by the braking system through any braking pedal or lever. This gives the driver better “feel” to avoid impending lockup.
Types:
Disc brake rotos are available in different styles; slotted, cross drilled, and vented are the most significant ypes. Each has a purpose, but replacing with the same type as the original is adcisable for most applications.
Damage:
Discs are commonly damaged in one of following ways: scarring, cracking, warping or excessive rusting. Service shops will respond to any disc problem by changing out the discs entirely, This is done mainly where the cost of a new disc may actually be lower than the cost of labour to resurface the old disc. Mechanically this is unnecessary unless the discs have reached manufacturer's minimum thickness recommondation, after which the usage is unsafe.
Common Tips:
Most leading vehicle manufacturers recommend disc turning as a solution for lateral run-out, vibration issues and brake noises. The machining process is performed in a brake lathe, which removes a very thin layer off the disc surface to clean off minued damages and restore uniform thickness. Machining the disc is necessary and will maximise the mileage out of the current discs on the vehicle.
Add Comment
Automobiles Articles
1. One Less Scrap, One More Solution: Turning Old Cars Into Opportunity In AucklandAuthor: Cars 4 Cash
2. Understanding The Chopper Trend- What It Looks Like
Author: Levi Fysh
3. Save Money On Car Repairs But Visiting Volkwagen Car Service
Author: Oliver Mertin
4. Be Sure Of These Things While Enrolling Your Name On A Driving School
Author: Eleanor Thompson
5. How To Maintain Jcb Hydraulic Couplings For Peak Efficiency
Author: Seetech Parts
6. Why Toyota Hiace Owners Trust Outback Exhausts For Dpf Solutions
Author: Seo Globo
7. Discover The Hidden Power Of Your Landcruiser 300 With This Exhaust Upgrade
Author: Seo Globo
8. Automotive Parts Manufacturing Costs Without Compromising Quality
Author: minda group
9. How To Shop Steering And Accelerator Cables For jcb
Author: Seetech Parts
10. Why High-quality Auto Parts Are A Must For Smooth Daily Driving: Top 6 Essentials
Author: minda group
11. Turn Your Unwanted Vehicle Into Instant Money: Auckland’s Smart Car Selling Solution
Author: Cars 4 Cash
12. Reliable Car Repair In Montreal: What You Need To Know
Author: meticulous montreal
13. Smarttop Convertible Top Control By Mods4cars Now Available For Ferrari Portofino M
Author: Mods4cars LLC
14. Corrosion Protection Strategies: Extending Leaf Spring Service Life
Author: sonicoleafsprings
15. Nfpa 610 – Prepare For Motorsport Emergencies – Rely On Nfpa 610 In The U.s. Today
Author: aurthorCole