ALL >> Business >> View Article
Vertical Roller Mills For Finish Grinding
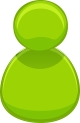
Vertical Roller Mills for Finish Grinding
With the continual increasing demand for portland cement and constant pressure for reduced energy consumption, producers are exploring a wide variety of cost-saving manufacturing options. One option is vertical roller mill technology for finish grinding.
Traditionally, plants used ball mills to grind clinker and gypsum into cement. The result: the majority (60%) of finish grinding in the world is still performed using the ubiquitous ball mill. Ball mills are cylindrical steel shells with steel liners. These rotating drums contain grinding media that tumble inside the cylinder. The grinding balls cascade and tumble onto the clinker and gypsum to produce cement. Almost all ball mills use a form of closed circuit grinding that returns material that is too coarse back to the ball mill inlet while material fine enough to meet product requirements is collected. The separator or classifier determines which particles will be returned and which particles are sufficiently fine. With an effort to increase production, ball mill physical size has increased almost to the physical limitation ...
... dictated by the gas velocities and accompanying pressures necessary for the process. Ball mills may not be the most efficient means of size reduction but their reputation for product consistency and their simplicity of operation have made them an historic plant favorite.
Since the 1980's, cement plants are increasingly looking to vertical roller mill technology for their finish grinding needs. Vertical roller mills present a compact and efficient grinding method. Clinker and gypsum is ground on a rotating table that passes under large rollers. Material is forced off the table by centrifugal force, where it is then swept up into an airstream to a classifier immediately above. Just as with a ball mill, material that is too coarse is returned to the table for additional grinding while material that is fine enough is collected as product. The compact design of a vertical roller mill allows it to dry, grind, and classify, all within one piece of equipment and all in a relatively compact space.
Vertical roller mill technology allows: (1) power consumption savings; (2) consistent product quality and (3) process simplification.
1. Cost Savings
The single largest energy consumption point in the manufacture of portland cement is in the finish milling process. A reduction in power consumption here makes a dramatic impact on the plant's overall power consumption. VRM technology makes significant power reductions possible by more efficient grinding.
2. Quality
Vertical roller mills create a particle size distribution with a sharper cut in comparison to cement milled in a traditional ball mill. That is, the particle size distribution is in a narrower band. This sharper cut means potentially less variability in product consistency and, hence, more predictable results in product performance.
3. Process Simplification
By changing various vertical roller mill operating parameters, significant adjustments in the particle size distribution, retention time, and fineness of the finished cement can be achieved. This can help with plant operations as production is switched between different cement types.
In light of these issues, vertical roller mills are becoming a popular choice for both existing ball mill conversion and new mill construction. From 2000-2002, 56% of the mill orders (comprising both raw mills and finish mills) came from vertical mills - compared to 32% for ball mills. Clearly vertical roller mills are an increasingly attractive option for improving production, lowering energy costs, and maintaining product quality.
websites:
jaw crusher
mobile crusher
stone crusher
ball mill
Add Comment
Business Articles
1. Seo Services For Small Business Indore: Boost Your Online PresenceAuthor: ayraphics
2. Women’s Tank Tops, Dresses, And Skirts In Encinitas, San Diego California
Author: Vikram kumar
3. Top Reasons To Use A Local Print Shop In San Francisco
Author: Bay Print Solutions
4. Quaker Oats Data Analytics On Amazon - The Oatmeal Deal Case Study
Author: Actowiz Metrics
5. Dubai Free Zone – A Hub For Business Growth And Global Opportunities
Author: David
6. What Is A Home Loan Calculator?
Author: Shreya Eppili
7. Using An Emi Calculator To Set Your Personal Loan Tenure During Application
Author: Shreya Eppili
8. Extract Wine Pricing Data Across Global Markets For Insights
Author: Den Rediant
9. Why A Tactical Picatinny Rail Forend Takes Your Remington 870 To The Next Level
Author: Slade Street Tactical
10. Powering Your Social Media Growth With Affordable Marketing Panels
Author: Smm Panel
11. Documenting Your Iso 50001 Procedures Effectively
Author: Sarah
12. Powering Progress With Quality Transformers– Kanyaka Parameshwari Engineering Pvt. Ltd
Author: Ojeshwani1
13. Cas No: 85118-00-9 Manufacturers
Author: vasista
14. How To Create Custom Clothing Online Without Compromising On Quality
Author: Guangzhou Beianji Clothing Co., Ltd
15. What Should You Know About Flat Roofing In Barrie?
Author: Ryan Seacrest