ALL >> Technology,-Gadget-and-Science >> View Article
Why Automotive Brands Are Adopting Qms Software Quickly?
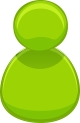
Early last year, German automotive giant BMW expanded a recall of its innovative “brake-by-wire” system from 80,000 to 1.5 million vehicles, including 7-Series sedans and XM SUVs, after intermittent signal losses risked total brake failure.
Not long before, the now-defunct Japanese automotive parts company Takata’s infamous airbag inflator defect resulted in sending over 100 million potentially explosive components under scrutiny in the largest safety action in U.S. history.
Closer home in India, Maruti Suzuki recently recalled 87,599 S-Presso hatchbacks and Eeco minivans over a steering-tie rod defect that compromised handling, while Honda India pulled back 92,672 City, Amaze, Jazz, WR-V, BR-V, and Brio models due to a faulty fuel pump risking engine stalls.
What Lessons Do We Learn From These Recalls?
These sweeping recalls underline the urgent need for a proactive Automotive Quality Management Software. They tell us that automotive businesses need a system that detects potential defects or failures early, streamlines ...
... the corrective actions, and keeps both manufacturers and the motorists safer.
These high-profile recall cases also share few common issues, i.e. gaps in process control, traceability, and risk management. For automotive brands, each recall not only results in massive repair bills and regulatory scrutiny, but also in huge blows to their brand reputation and customer trust.
That’s why an automotive quality software has become mission-critical for them. By centralizing document control, automating inspections, and integrating NC/CAPA, risk, and change-management workflows, a dedicated automotive QMS software platform helps manufacturers detect and resolve quality issues long before they escalate into mass recalls.
In the sections that follow, we’ll explore the key challenges auto-makers face today in the absence of an automotive quality management system, and how once such modern tool delivers the features and benefits needed to keep production lines safe, compliant, and on track.
The Cost of Skipping Automotive Quality Management Software
Automotive manufacturing demands precision at every turn. And what does that really mean? It means meeting strict regulations, juggling a global parts supply chain, and keeping pace with rapid innovations like EVs and ADAS.
And without a dedicated QMS for automotive industry, these top requirements quickly turn into vulnerabilities. Here’s how:
The Cost of Skipping Automotive Quality Management Software
Documentation Hassles: When key documents like the Standard Operating Procedures (SOPs), CAD drawings, design & validation reports, and supplier certificates are scattered across binders and network folders, audit delays, version mix-ups, and regulatory citations are bound to happen.
Cumbersome Change Management: Whether tweaking a battery pack design or issuing an ECU software update, manual email threads and handwritten sign-offs obviously slow approvals and obscure visibility, derailing production plans.
Reactive Risk & Recall Exposure: In the presence of manual methods, quarterly risk reviews are bound to miss emerging hazards. This mean a single faulty component, be it from electronics or rubber seals, can escape detection until it triggers a non-conformance or mass recall.
Inefficient NC/CAPA Workflows: Corrective and preventive actions turn into administrative chores when serious defects are logged in via paper forms and disparate emails. This eventually delays root-cause fixes and masks systemic quality issues.
Audit-Readiness Gaps: Disjointed data across quality metrics, training records, and inspection logs makes adherence to compliance a mission impossible, and this then reflects in audit findings or costly operational stoppages.
Unstructured Training Management: Without structured, automated training workflows, employee qualifications lapse without a notice. This results in new SOPs going unlearned, certifications expiring, and critical tasks falling to under-prepared staff.
Manual, Inconsistent Inspections: Paper checklists and ad-hoc reports create blind spots on the shop floor. Defects in key auto parts go unlogged, inspection schedules are missed, and defect trends remain invisible until it becomes too late.
Siloed Complaint Handling: Customer and dealer complaints routed by email or phone leave no traceable audit trail. Recurring issues slip through, leaving teams unable to identify patterns or implement preventive measures.
These challenges reveal why leading brands invest in QMS software for automotive industry, essentially to unify quality processes, automate training and inspections, centralize complaint management, accelerate corrective actions, and safeguard safety, compliance, and brand reputation from concept to customer.
How Automotive QMS Software Solves These Challenges?
A purpose‐built automotive quality management software like TecWork’s QualityPro eQMS software transforms these challenges into opportunities for operational excellence. How? Take a look:
Centralized Document Management & SOP Control:
An effective QMS software for automotive industry acts as a single source of truth for all quality documentation, including SOPs, CAD drawings, design reports, equipment manuals, validation protocols, and regulatory filings.
This ensures that only current, approved procedures guide production, while automated version control and electronic signatures simplify audit trails and reduce manual errors.
Streamlined Change & Risk Management:
A QMS solution’s integrated change control workflows route requests through predefined approval chains, while built‐in risk assessment workflows automatically trigger reviews when new data emerges, enabling proactive mitigation.
Automated NC & CAPA Tracking:
With a QMS system in place, NCs are logged directly in the system, generating CAPA tickets that flow seamlessly through investigation, root‐cause analysis, and corrective action tasks. Furthermore, real‐time progress indicators and effectiveness checks close the quality loop faster.
Digital Inspection & Audit Modules:
A QMS software’s digital inspection management checklists guide shop‐floor teams through quality checks for welding seams, paint thickness, and torque values, among others, while its compliance checklists aligned with IATF 16949, ISO 9001, and other standards come in handy for the auditors while conducting different types of audits.
Additionally, on‐the‐fly data capture and reporting eliminate paper forms and speed up audit preparation.
Comprehensive Training & Competency Management:
With a QMS software for automotive industry, training assignments, tied to specific SOPs or equipment, are dispatched automatically. Reminder notifications and competency tracking ensure that every team member completes mandatory modules before handling critical tasks.
Unified Complaint & Supplier Quality Management:
Also, with a QMS, customer complaints and supplier issue logs are fed directly into the system, enabling cross‐functional teams to analyze trends, initiate corrective actions, and maintain full traceability back to raw materials, components, or production batches.
By unifying these core functions, QMS software for automotive industry not only ensures compliance, but it also drives continuous improvement, cost savings, and faster innovation cycles.
Conclusion: Drive Quality Forward with QualityPro
In an industry where safety, compliance, and brand reputation hinge on flawless execution, having an automotive quality management software is no longer optional, it’s an absolute necessity.
A modern automotive QMS software like QualityPro unites document control, risk and change management, NC/CAPA, inspections, audits, training, and supplier quality into a single, easy-to-use platform.
Whether you’re producing internal combustion engines, electric vehicles, or advanced autonomy systems, TecWork’s QualityPro QMS system software got you covered. Write to our experts to schedule a demo and explore our solution, today.
Add Comment
Technology, Gadget and Science Articles
1. How Mobile App Development Service Enhances Customer Experience Across IndustriesAuthor: michaeljohnson
2. How Erp Solutions Help Manufacturers Increase Operational Efficiency
Author: Focus Softnet
3. Real-time Tim Hortons Menu And Price Tracking
Author: Real Data API
4. Industrial Automation In Europe: Strong 8.5% Cagr Through 2032
Author: Suvarna
5. Doordash Pricing Data Scraping Reveals Key Price Trends
Author: Retail Scrape
6. Retail Market Trends Shaped By Online Liquor Price Scraping
Author: Web Data Crawler
7. Benefits Of Less Common Laptop And Smartphone Brands
Author: John Rame
8. Finops In Practice: Controlling Costs In Cloud Migration Projects
Author: Matthew Hinge
9. How An Enterprise Ai Development Company Enhances Data-driven Decision Making
Author: michaeljohnson
10. Web Scraping Pet Food Data For Competitive Pricing
Author: Den Rediant
11. Top Mobile App Development Trends For Staying Ahead In The Digital Era
Author: Sdreatech
12. Real Estate Ai Agent For Investors: Data-driven Decision-making In Real Estate
Author: michaeljohnson
13. Mastering Java Operators
Author: jatin
14. How To Perform Audible Audiobook Data Extraction
Author: Real Data API
15. Plan, Control, Excel In Production Planning
Author: Focus Softnet