ALL >> Business >> View Article
Ms Chain: Safe Handling, Maintenance, And Inspection Best Practices
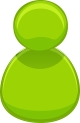
They are essential for lifting, securing, towing, and moving loads of varying sizes and weights. While chains are widely regarded for their strength and durability, they can pose significant risks if not handled properly. Adhering to proper handling techniques, conducting regular maintenance, and following thorough inspection protocols are vital steps in ensuring the longevity of chains and the safety of personnel involved in their operation.
This article explores the most effective methods for safe handling, outlines maintenance strategies that can extend the lifespan of chains, and highlights essential inspection practices to prevent accidents and equipment failure.
The Importance of Proper Handling
Chains are designed to endure substantial loads, but incorrect handling can compromise their structural integrity and lead to severe accidents. Understanding how to handle them correctly is the first step toward maintaining a safe working environment.
When moving chains, it is crucial to avoid dragging them across rough surfaces, as this can cause abrasions and weaken individual links. Sharp turns and twists ...
... during handling should also be avoided since they can introduce unnecessary stress points that may eventually lead to fractures or deformations. Additionally, operators should never subject chains to sudden jerks or shock loading. Sudden movements can significantly increase the force on the links, potentially exceeding their load capacity and causing unexpected breakages. Chains should always be lifted and lowered smoothly to distribute the load evenly.
Key Maintenance Practices for Longevity
Regular maintenance is fundamental to preserving the strength and functionality of chains over time. Chains that are neglected or improperly maintained are far more susceptible to premature wear and catastrophic failure. Chains often accumulate dirt, debris, and corrosive substances, especially in outdoor or industrial environments. Periodic cleaning using appropriate solvents and brushes can prevent build-ups that may lead to rust or interfere with movement. Lubrication is equally important. Proper lubrication reduces friction between links, minimizes wear, and protects against corrosion. Regular reapplication is necessary, especially in high-use or harsh conditions.
Detailed Inspection Procedures
Inspection is a critical component of chain safety. A comprehensive inspection routine can identify potential issues early and prevent dangerous failures during operations. Chains should be visually inspected before each use. Operators should look for obvious signs of damage, such as bent, cracked, or deformed links. Wear measurement is another essential aspect of inspection. Over time, chains naturally elongate due to stretching under load. Using precise measuring tools, operators should check whether the elongation exceeds allowable limits as specified by manufacturers. Excessive elongation reduces the load-carrying capacity and indicates that the chain may be approaching failure. Corrosion is a hidden hazard that can severely compromise the structural integrity of chains. Rust spots, pitting, and discoloration should not be overlooked. Chains showing significant corrosion should be retired or subjected to more detailed inspection by qualified professionals. In addition to the links themselves, attention must be given to accessories such as hooks, connectors, and shackles. These components are integral to the chain system and must also meet safety standards. Scheduled inspections by certified inspectors should be part of the maintenance plan, especially for chains used in critical or high-frequency lifting applications. Detailed inspection records should be maintained for each chain to track wear patterns and service history.
Common Causes of Chain Failure
Understanding why chains fail can help in both prevention and response. This can lead to instantaneous breakage or long-term fatigue. Improper angle of lifting is another frequent issue. Lifting chains at extreme angles creates uneven stress distribution, which can weaken certain links more rapidly than others. Environmental factors, such as exposure to chemicals, saltwater, or extreme temperatures, can accelerate corrosion and material degradation. Failing to account for these conditions during selection and use can drastically shorten the chain's lifespan. Poor maintenance, such as inadequate lubrication or neglecting regular cleaning, contributes to accelerated wear and frictional damage. Chains that are not periodically inspected may also fail without warning due to undetected cracks or fatigue.
Safety Guidelines for Chain Operations
To maximize safety and operational efficiency, a few universal guidelines should always be followed when working with chains. First, ensure that the load is evenly distributed across all links and that proper lifting angles are maintained. Second, chains should never be modified or repaired using makeshift methods. Only approved components and professional services should be used for adjustments or repairs. Third, proper training is essential. Operators should be familiar with load limits, lifting techniques, and emergency procedures in case of chain failure. Continuous safety education can significantly reduce human errors that lead to accidents. Lastly, signage indicating load limits, inspection schedules, and handling instructions should be displayed in work areas where chains are frequently used. These reminders help maintain a safety-first culture on site.
Conclusion
Chains, especially MS chain, are indispensable tools in lifting, securing, and material handling applications. However, their safe and effective use requires more than just strength; it demands proper handling, regular maintenance, and meticulous inspection.
By following best practices in each of these areas, operators can greatly extend the service life of MS chain while minimizing the risk of accidents and equipment failure. Ensuring that chains are used correctly and safely not only protects valuable assets but also safeguards the lives of those who rely on them every day. In high-risk environments, attention to detail and respect for safety procedures can make all the difference.
Add Comment
Business Articles
1. Remodeling Contractor Kitchen Secrets: Create A Space You’ll LoveAuthor: Scott
2. Lucintel Forecasts The Global Usb Wall Charger Market To Grow With A Cagr Of 6.2% From 2025 To 2031
Author: Lucintel LLC
3. Lucintel Forecasts The Global Tunnel Lighting Market To Grow With A Cagr Of 5.5% From 2025 To 2031
Author: Lucintel LLC
4. Lucintel Forecasts The Global Thyme Extract Market To Grow With A Cagr Of 6% From 2025 To 2031
Author: Lucintel LLC
5. Lucintel Forecasts The Global Tamper Evident Label Market To Grow With A Cagr Of 5.2% From 2025 To 2031
Author: Lucintel LLC
6. Lucintel Forecasts The Global Surface Cleaning Product Market To Grow With A Cagr Of 5.2% From 2025 To 2031
Author: Lucintel LLC
7. Why You Should Always Choose A Digital Business Card
Author: Angus Carruthers
8. The Virtual Receptionist Is An Asset For Your Business!
Author: Eliza Garran
9. Lucintel Forecasts The Global Supercritical Water Oxidation Technology Market To Grow With A Cagr Of 10.8% From 2025 To 2031
Author: Lucintel LLC
10. Strengthening The Future Of Production: The Role Of Manufacturing Supply Chain Solutions
Author: Trinity Diaz
11. Lucintel Forecasts The Global Sprocket Market To Grow With A Cagr Of 5.5% From 2025 To 2031
Author: Lucintel LLC
12. Price Benchmarking For D2c Brands With Ai Scraping | Actowiz Metrics
Author: Actowiz Metrics
13. What To Expect From The Inspection Company (tic)
Author: TIC
14. Budget-friendly Building Materials In Mumbai
Author: lTrikamdas
15. Digital Gold 2.0: The Case For Gold-pegged Crypto Stablecoins
Author: annagreyson