ALL >> Business >> View Article
Torque Calibration Services: Ensuring Precision And Safety In Applied Force
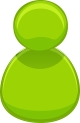
In industries where mechanical force plays a critical role—automotive, aerospace, manufacturing, construction, and energy—accuracy in torque measurement is essential. Torque, the measure of rotational force applied to a fastener or component, must be applied with precision to ensure equipment safety, product quality, and compliance with industry standards. Torque calibration services ensure that tools and devices used to apply torque deliver accurate and reliable results.
This article explores what torque calibration is, why it matters, the tools involved, how it’s performed, and the benefits it brings to various industries.
What is Torque Calibration?
Torque calibration is the process of verifying and adjusting the accuracy of torque tools—such as torque wrenches, screwdrivers, testers, and sensors—so they deliver consistent and accurate force. Over time, due to wear and tear, mechanical stress, and environmental conditions, these tools may lose accuracy, leading to under-tightening or over-tightening.
Calibration ensures the tool meets the manufacturer’s specifications and complies with ...
... relevant international standards, such as:
ISO 6789 – For torque tools
ISO/IEC 17025 – For calibration laboratories
NIST/NABL standards – National/international traceability
Why Torque Calibration is Important
Safety
Incorrect torque application can lead to loose connections or broken bolts, risking equipment failure or injury. Calibrated tools help prevent such hazards.
Product Quality
Many mechanical assemblies—especially in automotive and aerospace—require precise torque to function correctly. Even a slight deviation can lead to faulty products or operational failure.
Compliance
Industries must follow strict regulatory and quality standards. Torque calibration documentation is often required during audits and inspections.
Equipment Longevity
Properly torqued fasteners reduce strain on components, ensuring longer service life and reducing maintenance costs.
Cost Efficiency
Preventing product defects, rework, or field failures leads to significant cost savings over time.
Tools That Require Torque Calibration
A wide range of tools can be calibrated through professional torque calibration services, including:
Torque Wrenches (click type, beam type, dial type)
Torque Screwdrivers
Torque Multipliers
Torque Sensors & Transducers
Torque Testers & Calibrators
Pneumatic and Electronic Torque Tools
Calibration is typically done for tools used in production, quality control, field service, and research environments.
How Torque Calibration is Performed
Preparation & Inspection
The torque tool is visually inspected for damage, wear, or loose components. If repairs are needed, they’re performed before calibration begins.
Reference Standards
A master torque transducer or calibration system, certified by a national standards body (like NABL, NIST, or UKAS), is used to compare and verify the tool’s performance.
Testing Procedure
The tool is tested at multiple torque points across its range (usually 20%, 60%, and 100%). The readings are compared against the reference to determine accuracy.
Adjustment (if required)
If deviations are found, the tool is adjusted to bring it within acceptable tolerances.
Documentation
A detailed calibration certificate is provided, showing measurement data, traceability, uncertainty levels, and pass/fail status.
Labeling
Tools are labeled with calibration dates and due dates for easy tracking.
Frequency of Calibration
How often you calibrate a torque tool depends on:
Usage frequency
Tools used daily in production need more frequent calibration than those used occasionally.
Criticality of Application
Tools used in safety-critical applications (e.g., aircraft assembly) require more frequent calibration.
Manufacturer’s Recommendations
Follow guidelines provided in user manuals or technical datasheets.
Typical recommendation: Every 6 to 12 months, or after 5,000 cycles—whichever comes first.
Choosing a Torque Calibration Service Provider
When selecting a calibration lab or service provider, consider the following:
Accreditation
Choose providers accredited to ISO/IEC 17025 by NABL or an equivalent body. This ensures traceability and technical competence.
Capability Range
Ensure the lab can calibrate the specific torque range and tool type you use (e.g., from 0.1 Nm to 2,000 Nm).
Turnaround Time
Quick service is crucial for production environments. Ask about turnaround times and onsite calibration options.
Calibration Certificates
Verify that the certificates include all required data—uncertainty, traceability, tool ID, calibration points, and technician signatures.
Customer Support
Reliable technical support and reminder systems for recalibration dates can improve compliance and convenience.
Industries That Rely on Torque Calibration Services
Automotive Manufacturing & Repair
Aerospace and Defense
Electronics Assembly
Construction & Heavy Engineering
Oil & Gas
Railway and Marine
Renewable Energy (e.g., wind turbine assembly)
These industries demand high-precision fastening, making regular torque calibration a non-negotiable requirement.
Benefits of Regular Torque Calibration
Ensures consistent product quality
Reduces risk of mechanical failure
Improves safety in workplace and field use
Builds trust with clients and auditors
Extends tool life and reduces replacement costs
Keeps your operations compliant with ISO standards
Conclusion
In environments where mechanical accuracy matters, torque calibration is not just a best practice—it’s a necessity. Regular calibration of torque tools ensures safety, reliability, and compliance, giving organizations confidence in their processes and outputs.
By partnering with an accredited calibration service provider and maintaining proper records, industries can improve operational efficiency, reduce risk, and enhance product quality. Investing in torque calibration today ensures better performance and peace of mind tomorrow.
Add Comment
Business Articles
1. Most Expensive Places To Live In Dubai 2025: Top 14 Luxury AreasAuthor: luxury Spaces
2. Lucintel Forecasts The Phototherapy Lamp Market In Germany To Reach $1 Billion By 2031
Author: Lucintel LLC
3. Lucintel Forecasts The Percussion Instrument Market In United States To Reach $2 Billion By 2031
Author: Lucintel LLC
4. Lucintel Forecasts The Percussion Instrument Market In Japan To Reach $2 Billion By 2031
Author: Lucintel LLC
5. Gojek Clone App Script – A Complete Guide For Startups & Enterprises
Author: Swiza Joy
6. Lucintel Forecasts The Percussion Instrument Market In Germany To Reach $2 Billion By 2031
Author: Lucintel LLC
7. Web Design In The Age Of Ai: Opportunities And Challenges For Digital Marketers
Author: Vikram kumar
8. Lucintel Forecasts The Lung Cancer Surgery Market In United States To Reach $6 Billion By 2031
Author: Lucintel LLC
9. Salary Loans For Salaried Employees
Author: salarytopup
10. How Performance Testing Services Boost Software Quality
Author: Arnav Goyal
11. Byst: The Power Of Strong Business Mentors For Entrepreneurial Growth
Author: Byst Youth
12. How Iso 27001 Auditor Training Prepares Individuals For Internal Audits
Author: Jane
13. How To Sell My House Fast In Kentucky: A Homeowner's Guide?
Author: Adams Kirsten
14. Attractions And Living: Homes For Sale In Lexington, Ky
Author: Adams Kirsten
15. Trusted Old Coin Buyer: How To Sell Your Old Coins Safely In India
Author: surbhi