ALL >> Business >> View Article
How To Prepare For An Inspection Service Visit
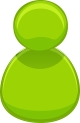
In the complex world of global manufacturing and supply chains, a third-party quality inspection is often the linchpin that ensures product integrity, mitigates risk, and protects brand reputation. For businesses, commissioning an inspection is a proactive step towards quality assurance. However, the effectiveness of this vital service hinges significantly on one often-overlooked factor: preparation.
At The Inspection Company, we’ve conducted countless inspections across diverse industries and geographies. While our experienced inspectors are adept at navigating various factory environments, the smoothest, most efficient, and ultimately most beneficial inspections are those where both the buyer and the supplier are well-prepared.
This blog post is designed to guide you – whether you are the buyer commissioning the inspection or the factory undergoing it – on How to Prepare for an Inspection Service Visit. Proper preparation isn't just about making the inspector's job easier; it's about maximizing the value you derive from the inspection, ensuring accurate results, and avoiding costly delays.
Why Preparation ...
... Matters
Before diving into the "how," let's briefly touch upon the "why." Why invest time and effort in preparing for an inspection?
✅ Accuracy of Results: The better prepared all parties are, the more accurate and comprehensive the inspection findings will be. Missing documentation or an uncooperative factory can lead to incomplete assessments.
✅ Efficiency and Timeliness: A well-prepared visit proceeds smoothly, minimizing delays. This saves time for both the inspector and the factory staff, ensuring reports are delivered promptly.
✅ Cost-Effectiveness: Delays and re-inspections due to poor preparation can incur additional costs. Proper preparation helps maximize the value of the initial inspection fee.
✅ Reduced Disputes: Clear expectations and readily available information reduce the likelihood of misunderstandings or disputes later on.
✅ Stronger Supplier Relationships: A factory that demonstrates preparedness shows professionalism and a commitment to quality, fostering a better working relationship with the buyer.
Preparing as the Buyer (Commissioning the Inspection)
As the buyer, you are the orchestrator. Your role is to provide clear instructions, relevant documentation, and ensure your supplier is aware of the inspection requirements.
1. Provide Comprehensive and Clear Instructions to Your Inspection Company
This is your most critical responsibility. The inspection company needs to know exactly what to look for.
✅ Detailed Product Specifications: This is paramount. Provide all technical specifications, drawings, dimensions, material compositions, color codes (Pantone, RAL, etc.), weight, and any specific performance criteria. The more detail, the better.
✅ Approved Samples: If there are golden samples or approved production samples, clarify whether the inspector needs to compare against these, and ideally, ensure the factory has them readily available.
✅ Quality Standards and AQL Level: Clearly state the Acceptable Quality Limit (AQL) level you require for the inspection (e.g., AQL 2.5/4.0). If you have specific quality criteria beyond AQL, document them.
✅ Test Methods: Specify any required in-house or third-party laboratory tests (e.g., tensile strength, flammability, chemical composition).
✅ Packaging and Labeling Requirements: Outline all requirements for inner packaging, master cartons, shipping marks, barcodes, and any specific warning labels.
✅ Shipping Marks: Provide the exact text and layout for shipping marks, ensuring consistency.
✅ Target Completion/Inspection Date: Communicate your desired inspection date and any flexibility.
✅ Order Details: Include the Purchase Order (PO) number, item numbers, quantities for each item, and any unique identifiers.
✅ Factory Contact Information: Provide full contact details for the factory representative who will assist the inspector.
2. Communicate Clearly with Your Supplier (the Factory)
Bridging the communication gap between the inspection company and the factory is key.
✅ Inform Them in Advance: Notify the factory about the upcoming inspection as early as possible. Provide them with the inspection company's name and contact details.
✅ Share All Relevant Documentation: Forward all the detailed specifications, quality standards, and packing requirements you provided to the inspection company to the factory. This ensures everyone is working from the same playbook.
✅ Explain the Purpose: Help the factory understand that the inspection is a collaborative effort aimed at ensuring quality, not merely a fault-finding mission. Frame it as a step to prevent future issues and build trust.
✅ Emphasize Readiness: Stress the importance of having goods ready for inspection, with necessary documentation available.
3. Define the Scope and Type of Inspection
Be clear about what kind of inspection you need.
✅ Pre-Production Inspection (PPI): Is it to verify raw materials and initial setup?
✅ During Production Inspection (DPI): To check progress and early defects?
✅ Pre-Shipment Inspection (PSI): The final check before shipment?
✅ Container Loading Inspection (CLI): To oversee loading?
✅ Factory Audit: To assess overall capabilities or social compliance?
This helps the inspection company allocate the right resources and prepare the appropriate checklist.
Preparing as the Supplier (the Factory Being Inspected)
For factories, a well-prepared inspection demonstrates professionalism, efficiency, and a commitment to quality. It can significantly streamline the process and avoid negative findings.
1. Understand the Scope and Requirements
Before the inspector even arrives, ensure you fully grasp what will be inspected.
✅ Review Buyer's Instructions: Carefully read and understand all specifications, quality standards (including AQL), test methods, and packing requirements provided by the buyer. If anything is unclear, ask for clarification immediately.
✅ Confirm Inspection Type: Know if it's a PPI, DPI, PSI, or other, as this dictates what needs to be ready.
✅ Anticipate Common Checks: Be aware of the standard checks performed during a typical inspection: quantity, workmanship, functionality, measurements, weight, color, labeling, packaging, and shipping marks.
2. Ensure Goods Are Ready and Accessible
This is perhaps the most common reason for delays or incomplete inspections.
✅ Complete Production (for PSI): For a Pre-Shipment Inspection, 100% of the goods must be produced and at least 80% packed. Do NOT request an inspection if production is not complete.
✅ Organize and Segregate Goods:
• Finished Goods: Have all finished goods (for PSI) or the required percentage (for DPI) moved to a designated, well-lit, and accessible inspection area.
• Defective vs. Good: Ensure any known defective units are clearly segregated from the units intended for inspection.
✅ Random Access: The inspector needs to be able to randomly select cartons. Do not stack them in a way that prevents random access to all parts of the lot.
✅ Provide an Adequate Workspace: Allocate a clean, well-lit, and sufficiently large area for the inspector to work, with a table, chairs, and access to power outlets if needed for testing equipment.
3. Prepare All Necessary Documentation
Having documents readily available saves immense time and avoids frustrating searches during the inspection.
✅ Purchase Order (PO): The original PO from the buyer.
✅ Product Specifications: All technical drawings, specifications, material lists, and approved golden samples/reference samples.
✅ Quality Control Records: Your internal QC reports, production checklists, and any test results conducted in-house.
✅ Packing List: A detailed list of carton contents, dimensions, and weights.
✅ Shipping Mark Details: Confirm the shipping marks match the buyer's requirements.
✅ Test Reports (if applicable): Any third-party lab test reports for raw materials or finished products.
✅ Previous Inspection Reports: If applicable, any reports from previous inspections.
4. Assign a Knowledgeable Point of Contact
Designate a responsible and knowledgeable staff member who will be available to assist the inspector throughout the visit.
✅ Authority: This person should have the authority to answer questions, retrieve documents, and facilitate access to different areas or personnel if needed.
✅ Language Skills: Ideally, this person should have sufficient English language skills (or a relevant common language) to communicate effectively with the inspector.
✅ Proactive Assistance: Encourage them to proactively assist the inspector, not just wait for requests.
5. Ensure Access to Necessary Equipment/Tools
The inspector may need to use certain factory equipment for testing or verification.
✅ Measuring Tools: Ensure access to calibrated measuring tapes, calipers, scales, etc., that can be used to verify dimensions and weights.
✅ Testing Equipment: If specific in-house tests are required (e.g., pull tests, voltage checks), ensure the relevant equipment is available and operational.
✅ Handling Equipment: For heavy goods, ensure forklifts or pallet jacks are available for moving cartons if necessary.
6. Be Prepared for Opening and Repacking
The inspector will need to open random cartons for visual inspection and re-pack them.
✅ Sealing Tape and Tools: Have packing tape, box cutters, and other necessary tools readily available for opening and re-sealing cartons.
✅ Assistance: Provide assistance for opening and re-sealing cartons, especially for large quantities.
The Day of the Inspection: What to Expect
Even with meticulous preparation, a smooth day-of execution is crucial.
✅ Welcome the Inspector: Greet the inspector promptly upon arrival and guide them to the designated inspection area.
✅ Initial Briefing: The factory representative and inspector should have a brief discussion to confirm the scope of work and clarify any immediate questions.
✅ Stay Available: The assigned point of contact should remain available throughout the inspection to answer questions and facilitate the process.
✅ Respect the Process: Allow the inspector to conduct their work independently and impartially. Avoid interference or pressure.
✅ Review Preliminary Findings: Towards the end of the inspection, the inspector will often provide a preliminary summary of findings. This is an opportunity to clarify any points.
Conclusion
A quality inspection is a powerful tool in quality control. By thoroughly preparing for an inspection service visit – whether you are the buyer or the supplier – you not only streamline the process but significantly enhance the accuracy and value of the inspection itself. This proactive approach fosters efficiency, prevents costly errors, safeguards your brand, and ultimately contributes to stronger, more reliable supply chain partnerships.
At The Inspection Company, we are dedicated to making the inspection process as seamless and effective as possible. By following these guidelines, you empower us to provide you with the most precise and actionable insights, ensuring your products consistently meet the highest standards.
Add Comment
Business Articles
1. Remodeling Contractor Kitchen Secrets: Create A Space You’ll LoveAuthor: Scott
2. Lucintel Forecasts The Global Usb Wall Charger Market To Grow With A Cagr Of 6.2% From 2025 To 2031
Author: Lucintel LLC
3. Lucintel Forecasts The Global Tunnel Lighting Market To Grow With A Cagr Of 5.5% From 2025 To 2031
Author: Lucintel LLC
4. Lucintel Forecasts The Global Thyme Extract Market To Grow With A Cagr Of 6% From 2025 To 2031
Author: Lucintel LLC
5. Lucintel Forecasts The Global Tamper Evident Label Market To Grow With A Cagr Of 5.2% From 2025 To 2031
Author: Lucintel LLC
6. Lucintel Forecasts The Global Surface Cleaning Product Market To Grow With A Cagr Of 5.2% From 2025 To 2031
Author: Lucintel LLC
7. Why You Should Always Choose A Digital Business Card
Author: Angus Carruthers
8. The Virtual Receptionist Is An Asset For Your Business!
Author: Eliza Garran
9. Lucintel Forecasts The Global Supercritical Water Oxidation Technology Market To Grow With A Cagr Of 10.8% From 2025 To 2031
Author: Lucintel LLC
10. Strengthening The Future Of Production: The Role Of Manufacturing Supply Chain Solutions
Author: Trinity Diaz
11. Lucintel Forecasts The Global Sprocket Market To Grow With A Cagr Of 5.5% From 2025 To 2031
Author: Lucintel LLC
12. Price Benchmarking For D2c Brands With Ai Scraping | Actowiz Metrics
Author: Actowiz Metrics
13. What To Expect From The Inspection Company (tic)
Author: TIC
14. Budget-friendly Building Materials In Mumbai
Author: lTrikamdas
15. Digital Gold 2.0: The Case For Gold-pegged Crypto Stablecoins
Author: annagreyson