ALL >> Business >> View Article
Top Challenges In Mixing Powders For Metallurgy And How To Overcome Them
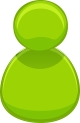
Summary
The manner of blending in powder metallurgy is fraught with challenges, but it's also one of the maximum important steps in determining the overall quality of the final product. From reaching homogeneous blends to stopping infection and retaining strict protection protocols, producers need to be vigilant at each turn.
Key challenges include particle segregation, powder agglomeration, contamination risks, and variable blending parameters. Each of these troubles can compromise the consistency and structural integrity of the parts produced. However, leveraging advanced mixing technologies, implementing particular running protocols, and preserving clean environments can move a long way in addressing these issues.
By completely knowledge the fundamental steps in powder metallurgy, especially how mixing integrates with compaction and sintering, manufacturers can ensure product reliability, lessen production defects, and enhance operational efficiency. Mastery of this level serves as a cornerstone for fulfillment in modern metallurgical production.
Mixing in powder metallurgy is a crucial step that ...
... drastically affects the nice and performance of the very last metal product. Despite its importance, many manufacturers face challenges at some point in the combination phase, which could cause inconsistent homes and manufacturing inefficiencies. Understanding those hurdles and getting to know how to address them efficiently is critical for all of us involved in powder metallurgy.
Powder metallurgy as a manufacturing approach entails numerous precise approaches, and combining is one of the most important among them. It guarantees uniform distribution of various powder parts, which at once influences the microstructure and mechanical properties of the finished product. To draw close the complexity of these challenges, it’s helpful to revisit the simple steps in powder metallurgy, which include powder guidance, mixing, compaction, and sintering. Proper mixing lays the inspiration for successful downstream processing.
Common Challenges in Mixing in Powder Metallurgy
1. Inhomogeneous Powder Blending
One of the largest problems in powder metallurgy is accomplishing a wonderfully homogeneous blend. Powders of different sizes, shapes, and densities tend to segregate, making it tough to hold uniformity. This segregation can lead to defects inside the final product, which include inconsistent density and mechanical weaknesses.
2. Contamination During Mixing
Contamination can occur from the environment, mixing gadgets, or operator handling. Even small amounts of contaminants can degrade the high-quality of the powder combo, main to defects or failure in the course of sintering or use. Maintaining clean, managed surroundings is crucial.
3. Powder Agglomeration
Some powders have a tendency to clump collectively all through mixing, growing agglomerates that don't break down without problems. This can bring about non-uniform blending and defects within the steel components and is a very important part of the basic steps in powder metallurgy. Preventing agglomeration requires optimized mixer design and sometimes the addition of waft retailers.
4. Inconsistent Mixing Times and Speeds
Using incorrect blending instances or speeds can result in underneath or over-mixing. Under-mixing outcomes in poor homogeneity, while over-blending can cause particle degradation or undesirable adjustments in powder characteristics.
5. Handling and Safety Issues
Powder metallurgy includes first-class powders that may be unsafe to deal with, consisting of the dangers of dust explosions or inhalation of harmful particles. Properly dealing with protocols and gadgets is important to ensure protection throughout blending.
How to Overcome These Challenges
Achieving Uniform Powder Blending
Using an advanced blending system like V-blenders, ribbon blenders, or high-energy mixers designed for metallurgy can help attain higher powder homogeneity. Regularly tracking particle size distribution and the usage of sieving strategies earlier than blending can decrease segregation troubles.
Preventing Contamination
Implementing strict cleanliness protocols, together with regular equipment cleansing and the usage of enclosed blending systems, reduces infection. Training operators on proper dealing with strategies is also critical.
Managing Powder Agglomeration
Incorporating flow dealers, which include graphite or lubricants, can reduce clumping. Selecting the right mixer kind and combining speed ensures powders stay frivolously disbursed without agglomerating.
Optimizing Mixing Parameters
Conducting trials to set up ideal blending instances and speeds for each powder combination ensures consistency. Automated mixers with programmable settings can preserve repeatability in large-scale manufacturing.
Enhancing Safety Measures
Using dirt collection systems, proper ventilation, and private defensive equipment (PPE) safeguards people. Additionally, following hints for flammable dirt management is vital.
Importance of Basic Steps in Powder Metallurgy
Powder metallurgy is a specialised production technique used to create metallic components with unique tolerances and precise fabric houses. The entire technique is structured around a few essential steps—every important to the achievement of the final product. These steps consist of powder production, mixing (or blending), compaction, sintering, and finishing. Among these, blending performs a pivotal role, acting as the bridge between powder guidance and element formation.
Understanding the fundamental steps in powder metallurgy enables highlighting how interdependent each segment is and why precision at each degree is non-negotiable. For example, throughout powder blending, specific metal powders and, once in a while, additives such as lubricants or binders are combined to ensure consistency in composition and flowability. This uniformity is critical, as it impacts how the powders behave throughout compaction—the degree to which pressure is applied to shape an 'inexperienced element.'
If the combination is inconsistent or improperly mixed, it could bring about density variations in the compacted part, leading to defects, together with cracking, warping, or insufficient electricity after sintering. During sintering, the compacted component is heated to a temperature below the melting point of the bottom metallic, allowing debris to bond at the molecular level. A properly mixed powder mixture guarantees steady shrinkage and mechanical properties across the complete batch of parts.
Moreover, the downstream finishing operations—like machining, surface remedy, or heat remedy—turn out to be smoother and greater predictable when the preliminary mixing is achieved efficiently. This step-by means of-step interdependence underlines why getting to know the fundamentals of powder metallurgy, particularly the mixing section, is so essential.
Conclusion
In today’s competitive manufacturing landscape, choosing the proper techniques and gadgets for blending in powder metallurgy is more than a high-quality practice—it’s a strategic necessity. High-quality powder mixing leads to advanced mechanical properties, dimensional accuracy, and consistency in mass manufacturing.
For manufacturers seeking to elevate their operations, the first step is frequently introspective: evaluating cutting-edge mixing methods, studying failure factors, and figuring out regions for development. Whether it includes upgrading to more superior mixing equipment, refining working processes, or enhancing best management measures, the goal is to set up a sturdy and repeatable mixing technique.
Proper training, periodic audits, and staying up to date with improvements in powder managing and mixing technology will offer a sizable competitive advantage. Simply put, making an investment of time and resources in learning the integration phase directly impacts profitability, consumer delight, and product integrity.
Are you equipped to take your powder metallurgy technique to the next level? Start by revisiting your existing workflow, and if needed, partner with experts or put money into contemporary gadgets to ensure you’re not leaving quality to chance. A small development within the blending section can result in enormous profits in universal production output and excellent.
For more details, please visit :- https://mim-supplier.com/
Add Comment
Business Articles
1. Remodeling Contractor Kitchen Secrets: Create A Space You’ll LoveAuthor: Scott
2. Lucintel Forecasts The Global Usb Wall Charger Market To Grow With A Cagr Of 6.2% From 2025 To 2031
Author: Lucintel LLC
3. Lucintel Forecasts The Global Tunnel Lighting Market To Grow With A Cagr Of 5.5% From 2025 To 2031
Author: Lucintel LLC
4. Lucintel Forecasts The Global Thyme Extract Market To Grow With A Cagr Of 6% From 2025 To 2031
Author: Lucintel LLC
5. Lucintel Forecasts The Global Tamper Evident Label Market To Grow With A Cagr Of 5.2% From 2025 To 2031
Author: Lucintel LLC
6. Lucintel Forecasts The Global Surface Cleaning Product Market To Grow With A Cagr Of 5.2% From 2025 To 2031
Author: Lucintel LLC
7. Why You Should Always Choose A Digital Business Card
Author: Angus Carruthers
8. The Virtual Receptionist Is An Asset For Your Business!
Author: Eliza Garran
9. Lucintel Forecasts The Global Supercritical Water Oxidation Technology Market To Grow With A Cagr Of 10.8% From 2025 To 2031
Author: Lucintel LLC
10. Strengthening The Future Of Production: The Role Of Manufacturing Supply Chain Solutions
Author: Trinity Diaz
11. Lucintel Forecasts The Global Sprocket Market To Grow With A Cagr Of 5.5% From 2025 To 2031
Author: Lucintel LLC
12. Price Benchmarking For D2c Brands With Ai Scraping | Actowiz Metrics
Author: Actowiz Metrics
13. What To Expect From The Inspection Company (tic)
Author: TIC
14. Budget-friendly Building Materials In Mumbai
Author: lTrikamdas
15. Digital Gold 2.0: The Case For Gold-pegged Crypto Stablecoins
Author: annagreyson