ALL >> Business >> View Article
The Fabric Inspection Process: A Step-by-step Breakdown
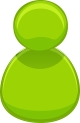
In the intricate world of textile and apparel manufacturing, the journey from raw fiber to a finished garment is long and multifaceted. Each stage presents opportunities for errors, but none is arguably more critical than the fabric inspection process. At RAQC Services, we understand that this is not just a formality; it's the bedrock of quality control, ensuring that the very foundation of a product—the fabric itself—meets the exacting standards required for customer satisfaction and brand reputation.
Imagine a beautifully designed dress, only to find a glaring flaw in the fabric once it's worn. Or a perfectly constructed pair of jeans with inconsistent shading. These seemingly minor issues, if unchecked at the fabric stage, can lead to significant waste, costly reworks, and ultimately, a damaged brand image. This is precisely why a meticulous fabric inspection process is indispensable. It acts as an early warning system, identifying and addressing potential issues before they become deeply embedded and expensive to rectify in the production line.
At RAQC Services, our fabric inspection process is designed ...
... to be comprehensive, systematic, and highly effective. Here's a step-by-step breakdown of how we ensure the quality of your fabrics:
Step 1: Preparation – Setting the Stage for Precision
Before any fabric roll is unrolled, proper preparation is crucial. This initial phase sets the groundwork for an accurate and efficient inspection.
✅ Environmental Control: Fabric inspection should occur in a well-lit, clean, and appropriately ventilated environment. Consistent lighting (often Cool White light, mimicking natural daylight) is vital to accurately assess color variations and subtle defects. The inspection table or machine should be positioned to ensure a viewing angle of 45-60 degrees for optimal visibility.
✅ Tools and Equipment: Essential tools include a fabric inspection machine (equipped with proper tension control and lighting), measuring tapes or calibrated rulers, defect tagging tools (stickers or markers), a GSM cutter (for weight checks), and a clear, detailed inspection checklist.
✅ Reference Materials: Crucially, approved bulk dye lot standards, physical samples of the approved fabric (for color, hand-feel, and construction comparison), and the client's specific quality specifications (including permissible defect points per standard yardage, width, and length tolerances) must be readily available.
Step 2: Sample Selection – Representing the Whole
It's rarely feasible or necessary to inspect 100% of every fabric roll. Therefore, a robust sampling plan is implemented to ensure a representative portion of the shipment is inspected. Common practices include:
✅ Random Selection: Rolls are randomly selected from the incoming lot to avoid bias. A minimum of 10% of the total yardage per shipment is often recommended, though this can vary based on the client's risk assessment and the type of fabric. For knitted fabrics, a minimum of 10% of rolls from each lot might be examined for weight.
✅ Early Inspection: Ideally, fabric inspection should commence when at least 80% of the good or lot has been received. This allows for a comprehensive assessment of the bulk production.
Step 3: Initial Verification – The First Glance
Once a roll is selected and mounted on the inspection machine, several initial checks are performed:
✅ Packaging and Identification: Verify that identification stickers, shipping marks, packing lists, and packing quantity align with the purchase order and specifications.
✅ Roll Integrity: Visually check the overall condition of the roll for any external damage, crushes, or signs of mishandling that could indicate internal fabric damage.
✅ Length and Width Verification: Carefully measure the length of the fabric against the supplier's ticketed tag. Any deviation is documented and reported. The fabric width is also checked from selvage to selvage against the specified standard, with any discrepancies noted.
✅ GSM (Grams per Square Meter) Check: For most fabrics, weight is a critical indicator of density, composition, and construction. A sample is cut using a GSM cutter and weighed accurately. This is compared against the specified GSM, ensuring the fabric meets the intended use requirements for warmth, durability, or comfort.
Step 4: Detailed Visual Inspection – The Core of the Process
This is where the majority of defects are identified. The fabric is unrolled at a controlled speed (typically not more than 15 yards per minute) across the lighted inspection table. The inspector meticulously scans the fabric for various flaws.
✅ Defect Identification: This involves looking for a wide array of defects, including:
• Weaving/Knitting Defects: Slubs, holes, broken ends/picks, missing yarns, barré marks (horizontal or vertical streaks), bowing (distortion of weft threads), skewing (diagonal distortion), mispicks, floats, coarse/fine yarn, tight/loose ends.
• Dyeing/Printing Defects: Shade variations (side-to-side, end-to-end, or within the roll), color bleeding, misprints, unlevel dyeing, streaks, patches, color spots, color bleeding, and shade continuity issues within a roll (checking shade variation between the center and selvage, and the beginning, middle, and end).
• Finishing Defects: Stains, oil spots, watermarks, creases, wrinkles, pilling, uneven finishes, odor (indicating chemical residue or improper processing), and hand-feel inconsistencies.
• Construction Defects: Inconsistent fabric density, irregular texture, or poor fabric hand (how it feels to the touch) compared to the approved sample.
✅ Defect Marking and Classification: When a defect is found, it is immediately flagged on the selvage (edge) of the fabric using a sticker or marker. Defects are classified based on severity and size, usually using a standardized system like the 4-Point System. This system assigns penalty points (1 to 4) based on the defect's length and impact, allowing for a quantitative assessment of fabric quality. Only major defects that would impact the final product are typically penalized.
✅ Repeat Measurement (for yard-dyed or printed fabrics): If the fabric has a pattern or print, the repeat measurement is taken at the beginning, middle, and end of selected rolls to ensure consistency.
Step 5: Performance and Lab Testing (as required) – Beyond the Visual
While visual inspection is crucial, certain quality parameters require laboratory testing to verify performance and compliance. These tests are conducted on selected samples from the inspected rolls.
✅ Colorfastness Tests: To assess how well the fabric retains its color when exposed to various conditions (washing, rubbing, light exposure, perspiration).
✅ Shrinkage Test: Measures how much the fabric changes in size and shape after washing. This is critical for garment fit and stability.
✅ Strength Testing: (e.g., tensile strength, tear strength, bursting strength) to evaluate the fabric's durability and resistance to breakage.
✅ Pilling Resistance Test: Assesses the fabric's propensity to form small balls of fiber on its surface (pills).
✅ Dimensional Stability Test: Measures how well the fabric retains its shape after washing or exposure to heat.
✅ pH Value and Harmful Substances: For certain applications, testing for pH balance, presence of azo dyes, formaldehyde content, and other restricted substances (e.g., in accordance with OEKO-TEX Standard 100 or REACH regulations) is vital for consumer safety and compliance.
✅ Fiber Composition Analysis: Verifies that the fabric's fiber content matches the label, often done through burn tests or chemical analysis.
Step 6: Documentation and Reporting – The Record of Quality
Every step of the inspection process is meticulously documented. This ensures traceability, accountability, and provides valuable data for continuous improvement.
✅ Detailed Inspection Report: This comprehensive report includes:
• Date of inspection, client, and supplier details.
• Fabric type, color, quantity inspected, and roll numbers.
• Detailed list of identified defects, their location, size, and assigned penalty points (e.g., using the 4-Point System score).
• Measurements taken (length, width, GSM) and any deviations from specifications.
• Results of any lab tests performed.
• Photographic evidence of major defects.
• Overall pass/fail status for each inspected roll and the entire lot based on the client's acceptance criteria (e.g., maximum allowable points per 100 square yards).
✅ Communication: The inspection report is promptly shared with the client and, if applicable, the supplier. This facilitates quick decision-making regarding acceptance, rejection, or necessary corrective actions.
Step 7: Decision and Action – From Inspection to Improvement
Based on the inspection report, the client can make informed decisions.
✅ Acceptance: If the fabric meets all specified quality standards and passes the inspection criteria.
✅ Rejection: If the fabric exhibits an unacceptable number of defects or fails critical performance tests, it is rejected, and a replacement from the supplier is often required.
✅ Remediation: In some cases, minor defects might be repairable (e.g., through mending or spotting) or manageable during the cutting and sewing stages, provided they are clearly marked.
✅ Feedback Loop: The inspection data provides crucial feedback to the fabric supplier, enabling them to understand and rectify issues at their source, leading to long-term quality improvement throughout the supply chain.
Conclusion
At RAQC Services, our seasoned inspectors combine technical expertise with a deep understanding of textile manufacturing. We don't just identify defects; we provide actionable insights and partner with our clients to optimize their supply chain and ensure their products consistently meet the highest quality benchmarks. By implementing this rigorous, step-by-step fabric inspection process, we help our clients minimize risks, reduce waste, and ultimately, deliver superior textile products to the market. Investing in thorough fabric inspection with RAQC Services is investing in the uncompromised quality of your final product.
Add Comment
Business Articles
1. Most Expensive Places To Live In Dubai 2025: Top 14 Luxury AreasAuthor: luxury Spaces
2. Lucintel Forecasts The Phototherapy Lamp Market In Germany To Reach $1 Billion By 2031
Author: Lucintel LLC
3. Lucintel Forecasts The Percussion Instrument Market In United States To Reach $2 Billion By 2031
Author: Lucintel LLC
4. Lucintel Forecasts The Percussion Instrument Market In Japan To Reach $2 Billion By 2031
Author: Lucintel LLC
5. Gojek Clone App Script – A Complete Guide For Startups & Enterprises
Author: Swiza Joy
6. Lucintel Forecasts The Percussion Instrument Market In Germany To Reach $2 Billion By 2031
Author: Lucintel LLC
7. Web Design In The Age Of Ai: Opportunities And Challenges For Digital Marketers
Author: Vikram kumar
8. Lucintel Forecasts The Lung Cancer Surgery Market In United States To Reach $6 Billion By 2031
Author: Lucintel LLC
9. Salary Loans For Salaried Employees
Author: salarytopup
10. How Performance Testing Services Boost Software Quality
Author: Arnav Goyal
11. Byst: The Power Of Strong Business Mentors For Entrepreneurial Growth
Author: Byst Youth
12. How Iso 27001 Auditor Training Prepares Individuals For Internal Audits
Author: Jane
13. How To Sell My House Fast In Kentucky: A Homeowner's Guide?
Author: Adams Kirsten
14. Attractions And Living: Homes For Sale In Lexington, Ky
Author: Adams Kirsten
15. Trusted Old Coin Buyer: How To Sell Your Old Coins Safely In India
Author: surbhi