ALL >> General >> View Article
Factors Affecting The Price Of Pre-engineered Metal Buildings
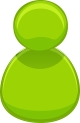
Pre-engineered metal buildings (PEMBs) have gained immense popularity in recent years due to their versatility, durability, and cost-effectiveness. From industrial warehouses and agricultural structures to commercial facilities and residential buildings, these buildings offer a wide range of benefits. However, like any construction project, the price of a pre-engineered metal building can vary significantly depending on several key factors. Understanding these factors can help developers and business owners make informed decisions when planning their construction projects. In this blog, we will explore the main factors that affect the price of pre-engineered metal buildings.
1. Size and Dimensions of the Building
One of the most significant factors influencing the price of a pre-engineered metal building is its size. The larger the building, the higher the overall cost, as more materials and labor are required. Pre-engineered metal buildings are priced per square foot or square meter, so the larger the area, the greater the total cost.
In addition to the basic floor area, the height of ...
... the building also affects the price. Taller buildings require additional steel and reinforcement, which increases the material cost. Whether you are building a small shed or a large industrial warehouse, the size of the structure will directly impact the price.
2. Materials Used
The materials chosen for the construction of a pre-engineered metal building can significantly affect the overall cost. The most common material used is steel, but the quality of the steel, as well as the specific type of metal (such as aluminum or galvanized steel), will influence the price.
Steel Quality: High-quality steel that is more resistant to corrosion and weathering will cost more but will offer greater durability in the long term.
Galvanization: Galvanized steel, which is coated with a layer of zinc to prevent rust, is more expensive than non-galvanized steel but is more durable in areas with high humidity or coastal climates.
Insulation: Adding insulation to the building's roof and walls will increase costs but improve energy efficiency, making the building more comfortable and lowering long-term utility bills.
The type and quantity of materials required for structural elements, such as beams, columns, and roofing panels, will also influence the cost.
3. Design Complexity and Customization
Pre-engineered metal buildings are often customizable to suit specific needs. While the base design is simple and modular, additional features or unique design elements can increase the price. Some of the design aspects that can affect the cost include:
Roof design: A pitched roof may cost more than a flat roof due to the additional materials and complexity.
Doors and windows: The number and size of doors and windows will increase the cost, particularly if custom-sized openings are needed.
Interior layout: Adding interior walls, partitions, or mezzanines to the building will raise the price as more materials and labor are required.
Specialized features: Elements like skylights, insulation, or additional support beams will add to the overall cost.
The more customized and complex the design, the higher the overall price.
4. Location and Site Conditions
The location of the building site plays a crucial role in determining the cost of a pre-engineered metal building. Site conditions such as soil quality, terrain, and accessibility can increase the cost of construction. For example:
Site Preparation: If the land needs to be cleared, leveled, or prepared in any way, these costs will be added to the total price. Challenging terrain or sites with poor soil conditions may require more extensive preparation or specialized foundations.
Transport Costs: The distance between the manufacturing plant and the building site affects transportation costs for delivering the pre-engineered components. The farther the distance, the higher the transport fees.
Local Regulations: Local building codes and regulations may require specific modifications to the design or materials, which can impact the cost. For example, buildings in areas with high wind or seismic activity may require reinforced structures or specialized designs to meet safety standards.
5. Labor Costs
Labor costs are a significant component of the overall price of a pre-engineered metal building. While pre-engineered metal buildings are designed to be easy to assemble, skilled labor is still required for assembly, welding, and installation. The cost of labor can vary based on several factors:
Labor Rates: Labor rates can differ by region and the skill level of the workers. In areas where skilled labor is in high demand, the cost may be higher.
Construction Time: The faster the construction timeline, the higher the labor costs. Delays, unexpected weather conditions, or complications during construction can increase the total cost of the project.
6. Shipping and Delivery
Pre-engineered metal buildings are often manufactured off-site and shipped to the construction site. The cost of shipping the materials can add to the total price, particularly if the site is far from the manufacturing location. Factors affecting shipping costs include:
Distance: The greater the distance between the manufacturing plant and the construction site, the higher the transportation costs.
Size and Weight of Components: The larger and heavier the pre-engineered components, the more expensive it will be to transport them.
Access to Site: Difficult-to-reach sites may require additional logistics or specialized equipment for delivery, which can increase costs.
7. Building Code Compliance and Permits
Each region may have its own set of building codes, zoning laws, and permit requirements. Compliance with these regulations may require modifications to the design or additional steps in the construction process, adding to the cost. For example, if the building needs to meet specific fire safety, structural, or environmental standards, additional materials or engineering services may be required.
Additionally, obtaining permits for construction can incur fees and delays, further affecting the overall price of the project.
8. Additional Features and Add-Ons
Many pre-engineered metal buildings can be fitted with additional features to enhance their functionality, comfort, and aesthetic appeal. These add-ons can increase the price of the building:
HVAC Systems: Heating, ventilation, and air conditioning systems can be added to improve indoor comfort, especially for commercial or industrial buildings.
Lighting and Electrical: Installing electrical wiring, lights, outlets, and other systems will increase the cost of the building.
Security Features: Features such as security doors, alarms, and surveillance systems can add to the overall price.
These optional features can be tailored to the specific needs of the building’s purpose, but each adds to the final cost.
Conclusion
The prefabricated buildings prices are influenced by a combination of factors, including the size and materials used, the complexity of the design, site conditions, labor costs, and additional features. Understanding these factors is crucial for estimating the cost of a project and making informed decisions about design, materials, and customization. By carefully considering each aspect, developers and business owners can ensure they get the best value for their investment in a pre-engineered metal building.
Add Comment
General Articles
1. Neotonics: A Comprehensive Review Of The Skin And Gut Health SupplementAuthor: Neotonics: A Comprehensive Review of the Skin and
2. Why Maintain Your Car Properly?
Author: Anthea Johnson
3. How Seva In Dharma Makes The World A Better Place
Author: Chaitanya Kumari
4. British And Irish Lions: Aunz V Lions Test Add On The Line
Author: eticketing.co
5. What Is Kpi And Kra? A Complete Guide To Performance Management Metrics
Author: TrackHr App
6. A Complete Guide To The Best Schools In Bhopal For Academic Excellence
Author: Ronit Sharma
7. British And Irish Lions 2025: Fans React To Shock Omissions
Author: eticketing.co
8. A Complete Guide To Installing Meter Boxes Safely And Correctly
Author: adlerconway
9. Your Shortcut To Smarter Learning
Author: coursefpx
10. Unencumber A Logo-new Way Of Life At Krisala 41 Commune Wakad: Wherein Luxurious Meets Clever Residing
Author: Armaan
11. Headless Wordpress As An Api For A Next.js Application
Author: brainbell10
12. Firebase And Crashlytics In Flutter And Swift
Author: brainbell10
13. Guide To Replacing And Maintaining Backhoe Loader Hydraulic Cylinders
Author: Seetech Parts
14. What Is The Difference Between On-grid, Off-grid, And Hybrid Solar Systems?
Author: Vishtik
15. Mobile Internet Usage Growth In Usa
Author: Jenny Knight