ALL >> Education >> View Article
Alloying Of Molybdenum
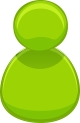
The alloying principle of molybdenum is similar to that of tungsten. All the strengthening methods used to improve the heat resistance of tungsten are basically applicable to molybdenum. There are mainly the following types: solid solution strengthening, precipitation strengthening, dispersion strengthening and composite strengthening.
Solution strengthening
Solid solution strengthening includes the addition of trace elements and high content elements.
The trace element solid solution strengthening method mainly refers to adding a trace amount of Ti, Zr, Fe, Mn, La, B and other alloy elements for solid solution strengthening to improve the performance of molybdenum. When trace elements are added, a certain amount of carbon is often added to the alloy. It is the alloy elements and carbon that form carbide dispersed particles to strengthen the strengthening effect.
High content element solid solution strengthening
The elements that improve the binding force between atoms of the molybdenum alloy and form a continuous solid solution are tungsten, tantalum, and rhenium. Tantalum and rhenium ...
... are scarce metals, the main alloy of solid solution strengthening with high content of elements is Mo-W alloy. The strength of the alloy increases with the increase of tungsten content, but its thermal deformation performance deteriorates with the increase of tungsten content, so the content of tungsten should not exceed 30%. The alloy has a very low ductility-brittle transition temperature due to the "rhenium softening effect". Commonly used molybdenum-rhenium alloys are Mo-5Re, Mo-41Re and Mo-50Re.
The solid solution strengthening alloy elements are mainly Ti, W, Re, and the typical alloys are Mo-0.5Ti, Mo-30W, Mo-41Re. The recrystallization temperature is 1100-1300℃, 1200℃, 1200-1300℃.
Molybdenum precipitation strengthening
The addition of titanium, zirconium and other active elements in molybdenum and the carbides generated by the reaction of carbon form a supersaturated solid solution during the high-temperature quenching of the alloy. This solid solution precipitates fine and dispersed titanium carbide and zirconium carbide particles during the subsequent annealing. Taking TZM alloy as an example, the alloy contains 0.40%-0.55% of titanium (mass fraction, the same below), zirconium 0.06%-0.12%, carbon 0.01%-0.04%, both titanium and zirconium are dissolved in molybdenum, solid solution strengthening It also reacts with the interstitial element carbon to form a compound titanium zirconium carbide. During the high-temperature quenching process of molybdenum alloys, the supersaturated solid solution formed during the subsequent annealing aging, this compound carbide forms precipitates as dispersed particles, which play a role in precipitation strengthening. The presence of oxygen (0.03%) in the alloy produced by the powder metallurgy method and titanium and zirconium forms a diffusely distributed spherical oxidized material point that is superior to carbides in inhibiting the growth of grains.
Among carbide-reinforced molybdenum alloys, TZM and TZC alloys have a very important position and have been widely used in industry application.
Molybdenum compound strengthening
(1) Oxidation strengthening. Al203, Mg0, ZrO2, etc. are commonly used strengthening molybdenum strengthening agents. In recent years,
Adding molybdenum to molybdenum to form an oxide dispersed phase can achieve the purpose of better strengthening the molybdenum alloy. The rare earth elements used are Y,
La, Ce, Nd, Sm and Cd, among which Y, Ce and La are the most commonly used, and the number of oxides they form in molybdenum is generally controlled
Controlled at about 1% (mass fraction).
(2) Doping strengthening (potassium bubble strengthening). The strengthening mechanism of doped K, Si and AI in molybdenum is basically similar to that of doped tungsten. After high temperature sintering, small potassium bubbles are formed in the matrix. During large plastic deformation and heat treatment, the potassium bubbles are alternately elongated and split into fine and dispersed rows of bubbles parallel to the direction of deformation, which delay the lateral growth of the grains. Large, forming dovetail lapped grains parallel to the deformation direction and highly elongated. The effect of A203 produced by doping is to ensure the effective potassium content, and SiO2 mainly plays a role in adjusting the grain size.
High-temperature molybdenum alloys MH (Mo-0.0015K-0.0029Si) and KW (Mo-0.002K-0.003Si-0.001Al) doped with K, Si, and Al are deformed to form tiny and dispersed potassium bubbles in molybdenum, so that the alloy has excellent creep resistance and extremely high recrystallization temperature, and the alloy still has good plasticity after recrystallization.
Molybdenum reinforced compound
The composite strengthening of molybdenum is to apply the above two or more strengthening mechanisms to molybdenum at the same time, so that molybdenum can obtain a better strengthening effect. Common compound reinforcements are
(1) Solid solution strengthening + precipitation strengthening. When 25% W is added to molybdenum, the melting point of the alloy increases by about 200°C. On the basis of MHC alloy and ZHM alloy, add 25% W to develop into M25WH (Mo-25W-1.0H-0.07C) alloy and M25WZH (Mo-25W-1.2Hf-0.4Zr-0.1C) alloy, at 1450℃, The tensile strength of the alloy reaches 750MPa.
(2) Dispersion strengthening + precipitation strengthening. Adding (0.8~1.0)% Y2O3 on the basis of ZHM alloy, the tensile strength of the alloy at 1450℃ is 40% higher than that of ZHM, which realizes the best combination of middle and high temperature application performance.
(3) Relay enhancement. For molybdenum alloys, the temperature range of solid solution strengthening is between 1100 and 1300°C, and it will fail at higher temperatures. The precipitation strengthening effect of carbide is most obvious at 1400~1500℃; in the range of 1500~1800℃, the stability of carbide becomes worse, and the dispersion strengthening effect of higher melting point rare earth oxide is remarkable. Above 1800°C, especially when it reaches 2000°C, the rare earth oxide begins to soften, resulting in a weakening of the strengthening effect, and the strengthening effect of potassium bubbles doped with K and Si is far more effective than other strengthening effects.
The development of composite strengthened alloys to achieve the effect of relay strengthening in different temperature zones is one of the directions for the development of high strength heat resistant molybdenum alloys.
Add Comment
Education Articles
1. Devops: The Modern Skillset Every Tech Professional Should MasterAuthor: safarisprz01
2. Salesforce Marketing Cloud Training In India | Cloud
Author: Visualpath
3. How An English Medium School Shapes A Child’s Future In Today’s Global World
Author: Mount Litera Zee School
4. Mern Stack Online Training In Ameerpet | Mern Stack Ai Training
Author: Hari
5. Why Online Courses In Sap Sd Are The Best Solution For Today's Professionals
Author: ezylern
6. Sailpoint Online Course In Bangalore For Professionals
Author: Pravin
7. Sap Ai Course | Sap Ai Online Training In Hyderabad
Author: gollakalyan
8. Why Aima Is The Best Choice For A Global Advanced Management Programme
Author: Aima Courses
9. The Best Oracle Integration Cloud Online Training
Author: naveen
10. Mlops Training Course In Chennai | Mlops Training
Author: visualpath
11. International Cbse School In Nallagandla,
Author: Johnwick
12. Best Mba Dual Specialization Combinations For 2025 And Beyond
Author: IIBMS Institute
13. Top Docker Kubernetes Training In Hyderabad | Docker And Kubernetestop Docker Kubernetes Training In Hyderabad | Docker And Kubernetes
Author: krishna
14. Full Stack Web Development Course In Noida
Author: Training Basket
15. Master Advanced Pega Skills With Pega Cssa Infinity'24.2 Online Training By Pegagang
Author: PegaGang