ALL >> Business >> View Article
Wire Harness Manufacturing Explain: Essential Electronics Lifelines
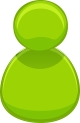
Wire harnesses, also known as cable harnesses, are the unsung heroes of the electronics world. These organized bundles of electrical cables act as the internal nervous system of countless devices, from simple appliances to complex automobiles and aeroplanes. They ensure the smooth flow of power and signals, keeping everything functioning as intended.
This article delves into the world of wire harness manufacturing, exploring the intricate processes behind these essential components. We'll uncover the steps involved, investigate the reasons for the prevalence of manual labour, and explore the future trends shaping this industry.
Guide to Wire Harness Manufacturing Journey: From Design to Delivery
The journey of a wire harness begins with meticulous design. Engineers translate the needs of the final product into detailed schematics, specifying wire types, lengths, connectors, and routing paths. This plan ensures the harness integrates seamlessly within the device, meeting all electrical and spatial requirements.
Prototyping follows design. Here, a small-scale version of the harness is built to test functionality ...
... and identify any potential shortcomings. This crucial stage helps refine the design before mass production commences.
With the design finalized, production commences. Here's a breakdown of the key steps involved:
Material Procurement: The manufacturing process starts with acquiring high-quality wires, connectors, terminals, and protective materials like sleeving or conduit. These components must adhere to strict specifications to guarantee reliable performance in the final product.
Wire Cutting and Stripping: Using specialized machines, wires are precisely cut to the designated lengths. The outer insulation is then carefully stripped to expose a specific amount of conductors for proper connection.
Terminal Attachment: The exposed conductor ends are prepped for connection by attaching terminals, pins, or other connector components using techniques like crimping, soldering, or welding.
Harness Assembly: Skilled technicians meticulously assemble the wires according to the design plan. This often involves routing the wires through designated paths, bundling them together using cable ties or lacing techniques, and ensuring proper strain relief at connection points.
Inspection and Testing: After assembly, each harness undergoes rigorous inspection to ensure all connections are secure, there's no physical damage, and the routing adheres to the design. Specialized electrical testing equipment verifies continuity, insulation integrity, and resistance to ensure the harness functions flawlessly.
Documentation and Packaging: Once a harness passes inspection, it's documented with relevant details like production date, batch number, and any specific test results. Finally, the harness is securely packaged for delivery to the final assembly line.
Also, Read: A Complete Guide to Mastering Wire Harness Manufacturing
The Enduring Role of Manual Labor
While automation plays a role in certain aspects of wire harness manufacturing, particularly in cutting, stripping, and testing, a significant portion of the process remains manual. This is primarily due to the high degree of customization inherent in wire harnesses.
Many devices require unique configurations, with varying wire lengths, connector types, and intricate routing paths. Manual assembly offers the flexibility needed to accommodate these diverse needs. Additionally, skilled technicians can identify and address potential issues during assembly, such as wire damage or routing conflicts, that might go unnoticed by automated systems.
However, the industry is constantly evolving. Advancements in robotics and machine vision are paving the way for more automation in wire harness assembly, particularly for high-volume production runs with less customization.
The Future of Wire Harness Manufacturing
The future of wire harness manufacturing is likely to witness a confluence of human expertise and automation. Here are some key trends on the horizon:
Increased Automation: As automation technologies advance, we can expect to see a rise in robots capable of handling more complex tasks in harness assembly. This could lead to faster production times and potentially lower costs for high-volume applications.
Improved Design Software: Advancements in design software will play a crucial role. These tools will streamline the design process, enabling engineers to create more intricate and optimized harness layouts, further enhancing functionality and manufacturability.
Focus on Miniaturization: The miniaturization trend in electronics will necessitate the development of even smaller and more intricate wire harnesses. This will require advancements in wire gauge, connector design, and assembly techniques to accommodate the reduced physical space.
Emphasis on Sustainability: As environmental consciousness grows, manufacturers will likely emphasise using eco-friendly materials and adopting sustainable practices throughout the wire harness manufacturing process.
In conclusion, wire harness manufacturing plays a critical role in bringing electronic devices to life. By understanding the intricate processes involved and the factors shaping the future of the industry, we gain a deeper appreciation for these essential components and the skilled professionals behind their creation. As technology evolves, wire harness manufacturing will continue to adapt and innovate, ensuring the smooth flow of information and power within the ever-expanding world of electronics.
For More Info: https://www.mefron.com/services/wire-and-cable-harness-manufacturing
Add Comment
Business Articles
1. Lucintel Forecasts The Global Satellite Operations As A Service Market To Grow With A Cagr Of 13.3% From 2025 To 2031Author: Lucintel LLC
2. Lucintel Forecasts The Global Satellite Operation As A Service Sale Market To Grow With A Cagr Of 13.5% From 2025 To 2031
Author: Lucintel LLC
3. Ticket Booking Api
Author: RishiHassan
4. Jewelry Photo Magic: Unveiling The Tricks Of Professional Editing
Author: ukclippingpath
5. How Outsourced Accounting Services Improve Cash Flow Visibility
Author: Harsh Vardhan
6. 5 Ways To Make Homes Safer For Seniors
Author: Jack Jones
7. اكتشفي أناقتك مع متجر عبايات: دليلك للتسوق المثالي
Author: Max
8. When Is Assisted Living Needed? 5 Signs To Watch Out For
Author: Jack Jones
9. How To Document Nonconformities In Iso 22000 Audits
Author: Jane
10. Elevate Your Career Opportunities With A Supply Chain Management Certification
Author: jayesh
11. Kpi Vs. Okr: Understanding The Difference For Smarter Goal Setting
Author: TrackHr App
12. Explore The Fascinating Businesses And Landmarks Found Along Luz Church Road
Author: jayesh
13. High Temperature Superconductors Market Size & Share, Analysis 2031
Author: Andy
14. Maximize Medical Practice Profits With Expert Revenue Cycle Management In Houston
Author: patriotmedbill
15. Enhancing Quality Of Life: The Role Of Senior Living Property Management Companies
Author: Trinity Diaz