ALL >> Business >> View Article
Fbe Coatings For Offshore Oil And Gas Pipelines:
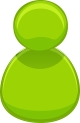
About Fusion Bonded Epoxy Coatings:
Fusion bonded epoxy coatings are made up of thermosetting resins and curing agents that, when applied to pipeline surfaces, cure to form a durable, protective layer. The coating is typically applied electrostatically and then cured in an oven, resulting in a seamless and durable barrier against corrosion. FBE coatings offer excellent adhesion to steel substrates, high chemical resistance, and superior mechanical properties. It makes them well-suited for offshore environments.
Benefits of FBE Coatings for Offshore Pipelines:
1. Corrosion Protection: The primary purpose of FBE coatings is to provide corrosion protection to offshore pipelines. The dense and water-resistant nature of the coating acts as a barrier. It prevents corrosive elements such as seawater and hydrogen sulfide from reaching the steel substrate. This helps extend the service life of the pipelines and reduces the need for costly maintenance and repairs.
2. Mechanical Strength: Fusion Bonded Epoxy Coating Plants exhibit excellent mechanical properties, including high impact resistance and flexibility. ...
... This is crucial for offshore pipelines, which may be subjected to external forces such as wave action, currents, and vessel impacts. The robust nature of FBE coatings helps maintain the structural integrity of the pipelines.
3. Temperature Resistance: Offshore pipelines often encounter fluctuations in temperature. It can range from subzero to high temperatures due to the transmission of hot fluids. FBE coatings can withstand a wide range of temperatures without compromising their performance.
4. Adhesion: Proper adhesion between the coating and the substrate is essential for long-term performance. FBE coatings form a strong bond with steel surfaces. Also, it provides excellent adhesion even in saltwater environments. This prevents delamination and maintains the protective layer's integrity over time.
Applications of FBE Coatings in Offshore Environments
FBE coatings find widespread applications in various components of offshore oil and gas infrastructure, including:
1. Subsea Pipelines: FBE coatings are commonly used to protect subsea pipelines from corrosion caused by seawater exposure. These pipelines transport crude oil, natural gas, and other hydrocarbons from offshore production platforms to onshore processing facilities.
2. Riser Systems: Risers are vertical pipelines that connect subsea wells to floating production platforms or fixed offshore structures. FBE coatings are applied to riser systems to safeguard against corrosion and maintain the structural integrity of these critical components.
3. Jackets and Substructures: Offshore platforms are supported by jackets and substructures installed on the seabed. FBE coatings are applied to these steel structures to prevent corrosion and extend their service life in the harsh marine environment.
4. Subsea Equipment: Various subsea equipment, such as manifolds, valves, and connectors, are protected with FBE coatings to enhance durability and reliability in offshore operations.
Advancements in FBE Coating Technology:
In recent years, significant advancements have been made in FBE coating technology to further enhance performance and address specific challenges in offshore applications. Some notable developments include:
1. Improved Formulations: The fusion bonded epoxy coating manufacturer has developed advanced FBE formulations with enhanced corrosion resistance, adhesion, and flexibility. They have been tailored to meet the demanding requirements of offshore pipelines.
2. Thermal Insulation: Certain FBE coatings are designed to provide thermal insulation, reducing heat loss and maintaining the temperature of transported fluids in subsea pipelines, especially in deepwater environments.
3. Cathodic Protection Compatibility: FBE coatings are now engineered to be compatible with cathodic protection systems, which further enhances corrosion protection by providing an additional layer of defense against corrosion.
Add Comment
Business Articles
1. Lucintel Forecasts The Global Wall-mounted Ac Ev Charger Market To Grow With A Cagr Of 22.4% From 2025 To 2031Author: Lucintel LLC
2. Technology Landscape, Trends And Opportunities In Global 3d Printing Photopolymer Market
Author: Lucintel LLC
3. Lucintel Forecasts The Global Smart Home Market To Reach $372 Billion By 2030
Author: Lucintel LLC
4. Second Marriage Matrimonial – Verified Matches & Free Registration
Author: Truelymarry
5. Core: Leading The Way In Managed It Services For Businesses Across London
Author: IT Management
6. The Role And Function Of A Collection Agency
Author: Bennett Carter
7. Understanding Debt Collection Agencies: What They Do And How They Affect Consumers
Author: Bennett Carter
8. How To Use An Smm Panel Effectively For Fast Social Media Growth
Author: Smm Panel
9. Essential Tips For Beginners And The Power Of Professional Editing
Author: Sam
10. How To Improve Field Staff Efficiency With Geolocation Tools
Author: TrackHr App
11. Building An Effective Energy Management System
Author: Jane
12. Internal Auditor Training: The Key To Effective Risk Management And Compliance
Author: Sqccertification
13. Why Accurate Accounting In Property Management Is The Key To Higher Roi
Author: Harsh Vardhan
14. Kaal Sarp Puja In Trimbakeshwar – Benefits, Process & Trusted Pandit Contact
Author: Pandit Milind Guruji
15. Data Entry Vs. Data Processing: What’s The Difference And Why It Matters
Author: Allianze BPO