ALL >> Business >> View Article
"din Flanges Demystified: A Comprehensive Overview"
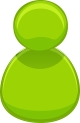
Introduction:
DIN flanges, integral components in industrial piping systems, adhere to the esteemed standards set by the German Institute for Standardization (DIN). This comprehensive guide aims to demystify the world of DIN flanges, focusing on key types such as Welding Neck, Threaded, Plate, Lapped, and Blind Flanges. Understanding the distinctive features and applications of each flange type is essential for engineers, project managers, and professionals working in fluid conveyance systems. Let's delve into the specifics of DIN flanges to illuminate their roles in ensuring efficient and reliable industrial operations.
1. DIN Welding Neck Flange:
Design: Featuring a tapered hub for welding, DIN Welding Neck Flanges provide a robust connection with pipes.
Applications: Ideal for high-pressure and high-temperature environments, offering stability and strength.
2. DIN Threaded Flange:
Design: With internal threads matching the pipe's external threads, DIN Threaded Flanges enable easy assembly and disassembly without welding.
Applications: Suitable for low-pressure systems, industries ...
... requiring quick assembly, and disassembly.
3. DIN Plate Flange:
Design: Flat and weldable or screwable, DIN Plate Flanges are cost-effective components often used with gaskets.
Applications: Common in low-pressure and non-critical applications, where simplicity meets functionality.
4. DIN Lapped Flange:
Design: Comprising a stub end welded to the pipe and a loose backing flange, DIN Lapped Flanges facilitate frequent dismantling for inspection or cleaning.
Applications: Valuable in systems with corrosion-resistant linings, offering adaptability and ease of maintenance.
5. DIN Blind Flange:
Design: Solid disks without a bore, DIN Blind Flanges effectively seal pipe ends or vessel openings.
Applications: Used to close off piping systems temporarily and in pressure vessel openings.
Conclusion:
As we navigate the diverse landscape of DIN flanges, from the robust Welding Neck Flanges to the versatile Threaded, Plate, Lapped, and Blind Flanges, it becomes clear that these components play a pivotal role in shaping the efficiency and reliability of industrial fluid conveyance systems. Engineers and professionals alike benefit from a nuanced understanding of each flange type, ensuring optimal selection based on the specific demands of their projects. This guide serves as a valuable resource for those seeking clarity in the realm of DIN flanges, fostering informed decision-making, and promoting excellence in industrial applications
Add Comment
Business Articles
1. Now Is The Time To Apply For A $1000 Same Day Payday LoansAuthor: Lucy Lloyd
2. Short Term Loans Online: A Vital Source Of Capital
Author: Robert Miller
3. The Benefits Of Acoustic Fencing For Residential And Commercial Properties
Author: Vikram kumar
4. Iso/iec 27001 Vs Iso/iec 27701: What Is The Difference Between Data And Privacy Security?
Author: Sqccertification
5. Why Local Seo Is The Lifeline For Small Businesses This Year
Author: Alpesa Media
6. The Power Of Authentic Vedic Rituals At Trimbakeshwar
Author: Shree Trimbakeshwar
7. Eicher 242 Tractor – A Small Tractor With Big Power For Indian Farmers
Author: KhetiGaadi
8. Top 10 Jewelry Editing Mistakes To Avoid For Perfect Shots
Author: ukclippingpath
9. Luxury Vacation Rentals In Nashville Tn
Author: Marcos Skyler
10. Top Booking Mistakes Hosts Should Avoid In Cabin Rentals
Author: Top Booking Mistakes Hosts Should Avoid in Cabin
11. The Importance Of Driveways In Multistory Building: Functionality, Safety, And Aesthetic Appeal Of A Building
Author: Vikram kumar
12. Rust Prevention Additives: The Amelioration Of Metal Protection Across All Industries
Author: Ivar
13. What Are Corrosion Inhibitors And Why Are Needed To Protect Metal Life?
Author: Ivar
14. Threaded, Socket Weld, Or Butt Weld? Choosing The Right Connection For Your Pipeline
Author: Online fittings
15. Mandatory Documents Required For Iso 45001 Certification
Author: Jenny