ALL >> Business >> View Article
Knowing The Fundamentals Of A Rotary Die Cutting Machine
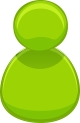
Introduction
In the modern production industry, efficiency, customization, and precision are critical. Modern technology has become essential to industries like electronics and packaging in order to satisfy customer needs. The rotary die cutting machine is one such piece of technology that has become indispensable in the manufacturing sector. We will go into the complex workings of rotary Die cutting machines, their uses, mechanics, and how they have transformed many industries in this in-depth guest post.
The Ingenious Mechanism Behind Rotary Die Cutting
Using a cylindrical die coated in specialised sharp blades or tools, rotary die cutting is an extremely complex and automated technique that can be used to cut, score, or perforate materials like paper, plastic, rubber, and even metal. The machine's core part, the die, rotates quickly while accurately shaping the material as it passes through. Examining the fundamental elements of rotary die cutting and their interrelationships is the first step towards comprehending ...
... its principles.
The Fundamental Parts of Rotary Die Cutting Equipment
Rotary Die: The cylindrical die itself is the central component of all rotary die cutting machines. This die is carefully tailored to meet the required cutting, scoring, or piercing specifications. Its size can vary. For durability against high-speed rotation and continuous use, premium steel or other strong materials are frequently used in its construction.
Anvil: The rotary die's cylindrical equivalent is the anvil. It guarantees cutting accuracy by supporting the material being cut and assisting in sustaining a steady pressure against the die.
Material Feed System: The raw material is fed into the machine by means of this material feed system. In order to facilitate cutting or shaping, it feeds the material into the nip point, which is the region where the rotary die and anvil come into contact.
Waste Removal System: To gather and eliminate the extra material produced during the cutting process, an integrated waste removal system is used. This lessens the need for manual clean-up by ensuring a tidy and effective operation.
Control Panel: Using the control panel, operators can enter and modify parameters such as the depth, cutting speed, and any particular patterns or shapes that need to be cut. It also offers a way to keep an eye on the machine's efficiency.
The Operational Concept of Rotary Die Cutting Machines
A continuous roll of material is fed into rotary ,Hot Foil Stamping Machine equipment and passes between the rotary die and the anvil. The material advances and comes into contact with the revolving die. The material is then cut or shaped according to the predetermined specifications by the sharp blades or tools on the die's surface. To guarantee precise, clean cuts, the anvil supports the cut and applies constant pressure.
The manufacturing rate is determined by the speed at which the material advances and the rotary die turns. The results are remarkably constant, and the entire process is extremely automated. The rotary die cutting machine is an essential tool in many sectors due to its quick conversion of raw materials into precisely formed and cut components.
Uses for Rotating Die Cutting
Because of its adaptability, rotary die cutting is a highly useful tool for a wide range of businesses, each of which gains from its special qualities. Among the well-known applications are:
Production of Labels and Stickers: Accuracy and uniformity are necessary in the label and sticker production process. Rotary die cutting is ideal for branding, product identification, and decorative labels since it guarantees that every label is the same size and shape.
Gasket Manufacturing: For accuracy and productivity, rotary die cutting is used in industries that depend on gaskets composed of materials like rubber or foam. With the highest precision, customised gaskets can be made to match certain applications.
Packaging Industry: To create unique packaging solutions, rotary die cutting is used in the packaging industry. To their precise specifications, manufacturers can produce complexly designed boxes, cartons, and packaging materials.
Medical Device Production: The medical sector uses rotary die cutting to make a variety of medical device components, including complex filters, sticky pads, and specialised packaging. Maintaining the integrity of medical items requires precise and clean incisions.
Electronics: Materials like plastic films and foams, which are essential to the creation of circuit boards, insulators, and other electronic components, are cut using a rotary die cutter in the electronics sector.
Automotive Sector: Gaskets, sound-absorbing materials, and customised interior parts are produced by manufacturers in this sector using rotary die cutting. One major benefit is the ability to precisely develop customised solutions.
Textile and clothing: To precisely cut textiles, leather, and other materials, the textile and clothing sector uses rotary die cutting. This is especially crucial when making clothing, upholstery, and accessories.
Aircraft: Gaskets, seals, and insulation materials are made in the aircraft industry using rotary die cutting. In these applications, accuracy and dependability are essential for guaranteeing the safety of aircraft parts.
Advantages of Die Cutting Using Rotary
When one understands the fundamentals of rotary die cutting, one can see the many benefits that this technology provides to many businesses. Among these advantages are:
Rotating die cutting machines are renowned for their remarkable accuracy and reliability. Ensuring high-quality final products is crucial in industries such as medical equipment and electronics, as every cut or shape is equal.
High Speed: Rotating die cutting machines' exceptional speed makes them perfect for large-scale manufacturing. Their ability to process materials fast and precisely increases manufacturing efficiency and shortens lead times.
Customization: Shapes, patterns, and designs can be fully customised using rotary die cutting. Because of its adaptability, it's the ideal choice for sectors that need specialised goods.
Decreased Material Waste: Rotating die cutting's efficiency reduces material waste. This reduces the quantity of scrap material produced throughout the manufacturing process, which not only helps with cost savings but also supports environmentally beneficial practises.
Enhanced Productivity: Rotating Die cutting machines lower labour costs and boost total productivity by automating the cutting and shaping process. Operators may concentrate on maintenance and quality control while the machine takes care of the monotonous duties.
Durability and longevity are ensured by the high-quality materials used to make the cylindrical dies used in rotary die cutting machines. For businesses, this means a dependable, long-term investment.
Consistency in Quality: Throughout the production process, rotary die cutting guarantees consistency in quality. In sectors where product integrity is critical, such as packaging and electronics, this is essential.
Conclusion
Working in the manufacturing, packaging, and allied industries requires people to understand the fundamentals of rotary die cutting equipment. several uses and several advantages are provided by this technology, including increased output, decreased material waste, and better product quality. As industries change, rotary die cutting is still a flexible and essential technology that helps companies succeed in a cutthroat market by producing large quantities of customised, high-quality products.
Add Comment
Business Articles
1. Lucintel Forecasts The Global Wall-mounted Ac Ev Charger Market To Grow With A Cagr Of 22.4% From 2025 To 2031Author: Lucintel LLC
2. Technology Landscape, Trends And Opportunities In Global 3d Printing Photopolymer Market
Author: Lucintel LLC
3. Lucintel Forecasts The Global Smart Home Market To Reach $372 Billion By 2030
Author: Lucintel LLC
4. Second Marriage Matrimonial – Verified Matches & Free Registration
Author: Truelymarry
5. Core: Leading The Way In Managed It Services For Businesses Across London
Author: IT Management
6. The Role And Function Of A Collection Agency
Author: Bennett Carter
7. Understanding Debt Collection Agencies: What They Do And How They Affect Consumers
Author: Bennett Carter
8. How To Use An Smm Panel Effectively For Fast Social Media Growth
Author: Smm Panel
9. Essential Tips For Beginners And The Power Of Professional Editing
Author: Sam
10. How To Improve Field Staff Efficiency With Geolocation Tools
Author: TrackHr App
11. Building An Effective Energy Management System
Author: Jane
12. Internal Auditor Training: The Key To Effective Risk Management And Compliance
Author: Sqccertification
13. Why Accurate Accounting In Property Management Is The Key To Higher Roi
Author: Harsh Vardhan
14. Kaal Sarp Puja In Trimbakeshwar – Benefits, Process & Trusted Pandit Contact
Author: Pandit Milind Guruji
15. Data Entry Vs. Data Processing: What’s The Difference And Why It Matters
Author: Allianze BPO