ALL >> Technology,-Gadget-and-Science >> View Article
Preparing For Injection Molding Resin Selection
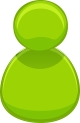
Manufacturers employ a diverse range of plastics for shaping components integrated into products, progressively replacing materials such as bronze, stainless steel, aluminium, and ceramics. This shift toward plastics is driven by several compelling factors, including extended part lifespan, reduced wear on other product components, enhanced production line efficiency, resistance to corrosion, and weight reduction. To ensure the successful production of a part, it is essential to collaborate closely with your best injection molding company when selecting the most suitable resin during the design for manufacturability phase. A good starting point is gaining a fundamental understanding of the two primary resin types: amorphous and semi-crystalline.
Amorphous
Amorphous resins encompass a variety of transparent plastics, including polycarbonate, acrylic, PETG, ABS, and polysulfone. This group of high-temperature resins can often serve as interchangeable substitutes within the same injection molds, as ...
... their linear shrinkage tendencies fall within a similar range.
Semi-crystalline
Semi-crystalline resins exhibit a highly organized molecular structure and do not undergo softening with increasing temperature; instead, they possess a well-defined and narrow melting point. Typically, their melting point surpasses the upper limit of amorphous thermoplastics. Nylon and Acetal are among the most frequently encountered semi-crystalline plastics.
Part Appearance and Geometry
The overall look and structure of a component have a significant influence on both the molding feasibility and the appropriate choice of resin. Aspects of part design, such as its dimensions, configuration, and wall thickness, can render it susceptible to imperfections. Additionally, features like snaps, undercuts, bosses, ribs, and more can introduce complexity into the molding process.
Recognizing the potential risks associated with part defects prior to commencing the manufacturing process represents a crucial step in injection molding. It is essential for plastic injection molding manufacturer to leverage cutting-edge technology to perform simulations that validate the design and resin selection before finalising the project for production.
Part Strength and Flexibility
The choice of materials plays a pivotal role in determining the strength and flexibility of your molded part. Achieving the optimal functionality of a part hinges on striking a balance between characteristics like stiffness, durability, toughness, and others. Additionally, it is crucial to comprehend the key distinctions among some of the more commonly employed resins.
ABS (acrylonitrile butadiene styrene) stands as a frequently used material for injection molding, readily available and moldable at a reasonable cost. It is a robust and sturdy material that offers commendable impact resistance, ease of machining, and meets various aesthetic demands. However, it is not suitable for applications involving sustained high temperatures, as it tends to warp or melt around 200 degrees Fahrenheit.
Polycarbonates belong to the high-grade category of thermoplastics, easily moldable and known for enhancing shatter resistance. With natural transparency, polycarbonate is ideal for applications requiring glass-like strength, such as safety goggles and medical lab equipment. Nonetheless, it may not be the best choice when flexibility or coloured aesthetics are paramount.
Glass-filled nylon is a reinforced thermoplastic, with added glass fibres to the base nylon resin to boost strength and heat resistance. This resin is also more electrically non-conductive compared to many others but is susceptible to burning despite its high melting point.
Polypropylene is a flexible thermoplastic suitable for both industrial and consumer applications. It is recognized for its high pliability, allowing it to be shaped in various ways without losing its original form. Polypropylene also offers resistance to solvents, chemicals, and UV rays.
Acetal is renowned for its excellent friction resistance and high rigidity. It can be easily coloured and dyed during the molding process, although it does not provide exceptional heat resistance.
Chemical and Environmental Factors
Many resins are susceptible to degradation when subjected to radiant and ultraviolet energy, which can lead to material breakdown. Extreme temperatures, humidity levels, radiation exposure, and other environmental variables, including potential requirements for fire resistance, all warrant consideration.
Regulatory Requirements
The plastic injection molding solutions and resin selection process can present unique challenges when it comes to meeting regulatory requirements. These criteria may encompass compliance with standards such as ASTM, ANSI, OSHA, FDA, EPA, and others.
Utilising Additives
The inclusion of additives can reinforce the materials, imparting strength and stiffness that can help minimise warping and shrinkage. Additives like glass or carbon fibres can be employed to elevate part performance and improve flow, ejection, and dispersion. This list should encompass essential considerations such as cost targets and resin availability, as resin availability can carry its own set of risks, necessitating the consideration of backup resin options. Factors like the array of available resins, part appearance, part strength, environmental considerations, regulatory demands, and the potential need for additives should all be meticulously evaluated before embarking on an injection molding project. Moreover, reviewing specifications for generic polymer variants is advisable, as these materials' characteristics may align well with your application.
If you are commencing a project that requires the expertise of an experienced plastic plastic injection mould manufacturer, discover how Moulding Injection aims to be your top-tier supplier and a reliable partner you can depend on.
Add Comment
Technology, Gadget and Science Articles
1. The Hidden Side Of Influencer Roi Nobody CalculatesAuthor: jatin
2. Cnc Machining In Medicine: Top Devices Shaping Modern Healthcare
Author: johan
3. Exploring The Multiple Benefits Of Hiring A Virtual Receptionist
Author: Eliza Garran
4. Virtual Answering Service- A Top Choice To Attain Success
Author: Eliza Garran
5. Track Flipkart & Amazon With Web Scraping For Price Insights
Author: Actowiz Solutions
6. How To Execute Naver Map Data Extraction For Business Listings Efficiently?
Author: Retail Scrape
7. Future Of Smart Ticketing: Global Market Analysis & Blockchain Innovations (2025–2032)
Author: Suvarna
8. Bid Export Api Integration For Inventory & Bids Management
Author: Retail Scrape
9. Dark Kitchen Location Data Scraping For New Brands
Author: Actowiz Solutions
10. Extract Global Listings For International Pricing Intelligence
Author: Actowiz Solutions
11. How To Backup Emails Without Any Hassle Or Data Loss?
Author: LIlywilson
12. Ensuring Compliance: Navigating Telecom Regulations With Advanced Ip Pbx Software
Author: Hodusoft
13. Coles Vs Woolworths: Fresh Produce Price Comparison
Author: Den Rediant
14. Can I Automate Business Workflows Using Salesforce Api Integration?
Author: Abhijith Rs
15. Simplifying Excellence: Why Awardocado Is The Ideal Award Management System
Author: Awardocado