ALL >> Business >> View Article
Top Tips For Successful Sheet Metal Bending
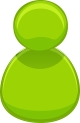
Top Tips for Successful Sheet Metal Bending
Introduction:
Sheet metal bending is a fundamental process in the fabrication of various products and structures. It involves deforming metal sheets to achieve desired shapes and angles. Whether you're a DIY enthusiast or a professional fabricator, understanding the basics of sheet metal bending techniques and acquiring some useful tips can help you achieve accurate and high-quality results. In this blog post, we will provide a comprehensive guide on sheet metal bending, along with valuable tips to enhance your bending skills.
Sheet metal bending is a process of deforming a sheet of metal into a curved shape. This is done by applying force to the metal, either manually or with the help of a machine. Sheet metal bending is a common process in metal fabrication, and it is used to create a wide variety of parts and components.
The Basics of Sheet Metal Bending
There are two basic types of sheet metal bending: cold bending and hot bending. Cold bending is a process that does not require heat, and it is typically used for thinner metals. Hot bending is a process ...
... that uses heat to soften the metal before it is bent, and it is typically used for thicker metals.
The amount of force required to bend sheet metal depends on the type of metal, the thickness of the metal, and the radius of the bend. The force is typically applied by a machine, but it can also be applied manually with the help of a bending tool.
Understanding the Basics of Sheet Metal Bending:
Sheet metal bending involves applying force to a metal sheet to form it into a specific shape or angle. The process typically utilizes a press brake machine, which consists of a punch and a die. The punch exerts pressure on the sheet metal against the die, causing it to bend along a predetermined line. The line where the metal bends is called the bend line, and it should be properly positioned to achieve the desired shape.
Selecting the Right Tools and Equipment:
Choosing the appropriate tools and equipment is crucial for successful sheet metal bending. A high-quality press brake machine with accurate bending capacity is essential. Additionally, consider using specialized tools such as bending jigs, clamps, and measuring devices to ensure precision and repeatability. Having the right tools at your disposal enhances efficiency and improves the quality of your bends.
Material Selection and Preparation:
Different types of sheet metals exhibit varying bending characteristics. Common materials include mild steel, stainless steel, aluminum, and brass. It's important to understand the properties of the specific metal you are working with, such as its thickness, ductility, and springback tendency. Prepare the metal by ensuring it is clean, free from debris, and properly lubricated to minimize friction during bending.
Determining Bend Allowance and Bend Deduction:
Bend allowance and bend deduction are essential calculations in sheet metal bending. Bend allowance refers to the length of material consumed during bending, while bend deduction accounts for the elongation of the material due to bending. Accurate calculations of these parameters help determine the correct dimensions of the flat pattern before bending, ensuring precise final part dimensions.
Proper Technique for Sheet Metal Bending:
When performing a bend, align the sheet metal accurately with the bend line on the press brake. Apply consistent and gradual pressure using the punch to avoid material deformation or damage. Ensure the material is properly supported to prevent unwanted flexing or distortion during bending. Practice good hand placement and control to maintain stability and accuracy throughout the process.
Overcoming Springback:
Springback refers to the tendency of the metal to return to its original shape after bending. It is influenced by factors such as material type, thickness, and bending angle. To overcome springback, consider adjusting the bend angle slightly beyond the desired final angle. Compensating for springback ensures the final bent part matches the intended specifications.
Quality Control and Finishing:
Inspect each bent part for accuracy and quality. Use measuring tools like calipers or angle finders to verify dimensions and angles. Pay attention to any defects such as cracks, wrinkles, or uneven bends. Additionally, consider post-bending processes like deburring or surface finishing to enhance the aesthetics and functionality of the final product.
Tips for Sheet Metal Bending
Here are some tips for sheet metal bending:
• Always use the correct tools and equipment for the job.
• Use a bending tool that is the correct size for the metal you are bending.
• Apply the force evenly to the metal.
• Do not bend the metal too sharply, or it may crack.
• Allow the metal to cool completely before removing it from the bending tool.
Common Problems in Sheet Metal Bending
There are a few common problems that can occur when bending sheet metal. These problems include:
Cracking: This can occur if the metal is bent too sharply or if the force is applied unevenly.
Warping: This can occur if the metal is not supported properly during bending.
Springback: This is the tendency of the metal to return to its original shape after it is bent.
How to Avoid Common Problems in Sheet Metal Bending?
To avoid common problems in sheet metal bending, it is important to follow these tips:
• Use the correct tools and equipment for the job.
• Use a bending tool that is the correct size for the metal you are bending.
• Apply the force evenly to the metal.
• Do not bend the metal too sharply.
• Allow the metal to cool completely before removing it from the bending tool.
Conclusion:
Sheet metal bending is a fundamental skill in metal fabrication, and mastering the techniques can greatly enhance your capabilities as a fabricator. By understanding the basics, selecting the right tools, and applying proper techniques, you can achieve precise and high-quality bends in various sheet metal projects. Remember to consider material properties, perform accurate calculations, and overcome challenges like springback. With practice and attention to detail, you can elevate your sheet metal bending skills and create outstanding metal components and structures.
Sheet metal bending is a versatile process that can be used to create a wide variety of parts and components. By following the tips in this blog, you can avoid common problems and produce high-quality bends.
MetalForming, LLC. is the industry expert and metal forming equipment distributor in sheet metal folding & fabrication sheet metal machinery application in architectural & precision fabrication. https://www.metalforming-usa.com/
Add Comment
Business Articles
1. Lucintel Forecasts The Global Wall-mounted Ac Ev Charger Market To Grow With A Cagr Of 22.4% From 2025 To 2031Author: Lucintel LLC
2. Technology Landscape, Trends And Opportunities In Global 3d Printing Photopolymer Market
Author: Lucintel LLC
3. Lucintel Forecasts The Global Smart Home Market To Reach $372 Billion By 2030
Author: Lucintel LLC
4. Second Marriage Matrimonial – Verified Matches & Free Registration
Author: Truelymarry
5. Core: Leading The Way In Managed It Services For Businesses Across London
Author: IT Management
6. The Role And Function Of A Collection Agency
Author: Bennett Carter
7. Understanding Debt Collection Agencies: What They Do And How They Affect Consumers
Author: Bennett Carter
8. How To Use An Smm Panel Effectively For Fast Social Media Growth
Author: Smm Panel
9. Essential Tips For Beginners And The Power Of Professional Editing
Author: Sam
10. How To Improve Field Staff Efficiency With Geolocation Tools
Author: TrackHr App
11. Building An Effective Energy Management System
Author: Jane
12. Internal Auditor Training: The Key To Effective Risk Management And Compliance
Author: Sqccertification
13. Why Accurate Accounting In Property Management Is The Key To Higher Roi
Author: Harsh Vardhan
14. Kaal Sarp Puja In Trimbakeshwar – Benefits, Process & Trusted Pandit Contact
Author: Pandit Milind Guruji
15. Data Entry Vs. Data Processing: What’s The Difference And Why It Matters
Author: Allianze BPO