ALL >> Technology,-Gadget-and-Science >> View Article
An Overview Of Industrial Control Systems: Ensuring Efficiency And Safety In Industrial Environments
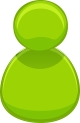
In today's technologically advanced world, industries rely heavily on automated systems to streamline operations and maximize efficiency. Industrial Control Systems (ICS) play a crucial role in managing and controlling industrial processes, from manufacturing plants to power grids. This article provides a comprehensive overview of industrial control systems, their components, key functionalities, and their significance in ensuring operational efficiency and safety in industrial environments.
Understanding Industrial Control Systems
Industrial Control Systems are specialized computer-based systems designed to monitor, control, and automate various industrial processes. They integrate hardware and software components to collect data, make real-time decisions, and regulate industrial equipment. ICS is responsible for managing critical infrastructure sectors such as energy, water, transportation, and manufacturing.
Components of Industrial Control Systems
1. Supervisory Control and Data Acquisition (SCADA): SCADA systems are the central hub of an ICS. They monitor and control processes using ...
... a network of sensors, remote terminal units (RTUs), and programmable logic controllers (PLCs). SCADA systems provide real-time data visualization, and historical data logging, and enable remote control of industrial processes.
2. Programmable Logic Controllers (PLCs): PLCs are ruggedized computers that control the operation of industrial machinery and equipment. They receive input from sensors, process it using pre-programmed logic, and generate output signals to control actuators and devices. PLCs are widely used in manufacturing plants, power generation facilities, and other industrial sectors.
3. Human-Machine Interface (HMI): HMIs provide a graphical interface for operators to interact with and monitor industrial processes. They display real-time data, and alarms, and enable operators to issue commands or adjust control parameters. HMIs enhance situational awareness and facilitate efficient decision-making.
4. Communication Networks: Industrial control systems rely on robust communication networks to transmit data between different components. These networks can be wired or wireless, depending on the specific requirements of the industrial environment. Industrial Ethernet, Fieldbus protocols, and wireless technologies like Wi-Fi and cellular networks are commonly used for data transmission.
Functionality and Importance of Industrial Control Systems
1. Process Automation: ICS automates repetitive tasks, enabling consistent and accurate execution of industrial processes. This improves productivity, reduces human error, and optimizes resource utilization.
2. Remote Monitoring and Control: ICS allow operators to monitor and control industrial processes remotely, ensuring continuous operation and reducing the need for on-site presence. This enhances operational flexibility and efficiency.
3. Fault Detection and Diagnostics: Industrial control systems include advanced algorithms and analytics to detect anomalies, identify faults, and provide diagnostics. Early detection of issues enables timely intervention, minimizing downtime, and optimizing maintenance activities.
4. Safety and Security: ICS incorporates safety measures and protocols to ensure the protection of personnel, equipment, and the environment. They implement security measures to protect against cyber threats and unauthorized access to critical systems.
5. Data Collection and Analysis: Industrial control systems collect vast amounts of data from sensors and equipment, which can be analyzed to identify trends, optimize processes, and make informed decisions for continuous improvement.
Challenges and Future Trends
While industrial control systems offer numerous benefits, they also present challenges. These include ensuring cybersecurity, managing system complexity, and addressing compatibility issues. Future trends in ICS include the integration of Artificial Intelligence (AI) and Machine Learning (ML) for predictive maintenance, increased use of edge computing for real-time decision-making, and the adoption of the Industrial Internet of Things (IIoT) for enhanced connectivity and data exchange.
Conclusion
Industrial Control Systems are the backbone of modern industrial environments, enabling efficient and safe operations. Understanding the components, functionalities, and significance of ICS is crucial for industries to harness their full potential. With advancements in technology, industrial control systems will continue to evolve, driving innovation and transforming industrial processes for years to come.
Add Comment
Technology, Gadget and Science Articles
1. The Hidden Side Of Influencer Roi Nobody CalculatesAuthor: jatin
2. Cnc Machining In Medicine: Top Devices Shaping Modern Healthcare
Author: johan
3. Exploring The Multiple Benefits Of Hiring A Virtual Receptionist
Author: Eliza Garran
4. Virtual Answering Service- A Top Choice To Attain Success
Author: Eliza Garran
5. Track Flipkart & Amazon With Web Scraping For Price Insights
Author: Actowiz Solutions
6. How To Execute Naver Map Data Extraction For Business Listings Efficiently?
Author: Retail Scrape
7. Future Of Smart Ticketing: Global Market Analysis & Blockchain Innovations (2025–2032)
Author: Suvarna
8. Bid Export Api Integration For Inventory & Bids Management
Author: Retail Scrape
9. Dark Kitchen Location Data Scraping For New Brands
Author: Actowiz Solutions
10. Extract Global Listings For International Pricing Intelligence
Author: Actowiz Solutions
11. How To Backup Emails Without Any Hassle Or Data Loss?
Author: LIlywilson
12. Ensuring Compliance: Navigating Telecom Regulations With Advanced Ip Pbx Software
Author: Hodusoft
13. Coles Vs Woolworths: Fresh Produce Price Comparison
Author: Den Rediant
14. Can I Automate Business Workflows Using Salesforce Api Integration?
Author: Abhijith Rs
15. Simplifying Excellence: Why Awardocado Is The Ideal Award Management System
Author: Awardocado