ALL >> Business >> View Article
Steps To Implement Poka Yoke Management
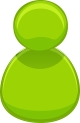
In the early 1960s, Shingo observed that workers were forgetting to insert springs in a simple on/off switch. This one small error resulted in faulty parts being manufactured and shipped. From his observations, Shingo learned that Sometimes people forget to do things.
Knowing that these simple human mistakes were the root cause of the issue, Shingo started working on ways to enhance the procedures and to make it an idiot-proof. After a worker complained that the term was abusive, he changed it to poka-yoke, which shifts the attention from the worker to the procedure. By redesigning the procedures so that the operation could not proceed until the worker had injected the spring into the switch, fewer human mistakes were made and higher quality products were shipped.
How to implement poka-yoke?
Implementing poka-yoke should be easy, low-cost, and associated with current procedures. Organization should see instant benefits and measurable developments in quality and production. Organization can implement poka-yoke by using the steps described below.
Identify the issue: Remember that humans make mistakes. One ...
... or two mistakes are to be predictable. A sequence of mistakes specifies that there is an issue that wants to be addressed. That issue may be with the employee or with a fault in a machine. Essential to observe the procedures to see if it can identify where the issue is happening. Enlist the help of others to determine whether the mistake is human or mechanical.
Find the root cause: After identify the issue, organization will need to determine what is the most likely reason of that issue. Organization may need to consider using the 5 Whys, another quality control technique established in Japan, it helps to find the root cause. By asking and answering five “why” questions, organization will dig down to find the root cause of the issue.
Determine which type of poka-yoke to use: If you can easily stop mistakes from happening, install a control poka-yoke that stops the procedures from remaining until a crucial step is accomplished. If the shape of a component confirms that it can only be implanted in the correct way. If you can’t stop a mistake, install a warning poka-yoke that alerts the operator that attention is required before the procedure can continue. These warnings can contain colors, flashing lights, buzzers, or any type of alerts that tell the employee that something wants to happen before the procedure continues.
Determine the most suitable poka-yoke method to use: There are three poka-yoke methodologies organization can choose from.
• Contact: This method uses shape, size, or other physical features to identify mistakes.
• Constant number: With this method, mistakes are triggered if a specific number of actions are not made. The operator is warned if the wrong number of moves are made.
• Sequence: This method confirms that the correct sequence of events is followed before a procedure can continue.
Test poka-yoke system: Before completely implement a poka-yoke, organization need to assure that it will work. Organization must test it to see if the mistakes is prohibited and to make sure that the fix does not slow down the procedure.
Train employees: Even the simplest poka-yoke can’t be successfully implemented until employees are trained how to do it. Poka Yoke Management Training helps with employee acceptance of the new procedure, especially if they can see that the fix makes their job easier to do. Add new poka-yoke to SOP guide to help employees understand what is expected of them.
Review performance and measure success: Observe the procedure again and measure success. Begin looking for other mistakes that may be impeding production and look for ways to constantly improve.
Add Comment
Business Articles
1. Seo Services For Small Business Indore: Boost Your Online PresenceAuthor: ayraphics
2. Women’s Tank Tops, Dresses, And Skirts In Encinitas, San Diego California
Author: Vikram kumar
3. Top Reasons To Use A Local Print Shop In San Francisco
Author: Bay Print Solutions
4. Quaker Oats Data Analytics On Amazon - The Oatmeal Deal Case Study
Author: Actowiz Metrics
5. Dubai Free Zone – A Hub For Business Growth And Global Opportunities
Author: David
6. What Is A Home Loan Calculator?
Author: Shreya Eppili
7. Using An Emi Calculator To Set Your Personal Loan Tenure During Application
Author: Shreya Eppili
8. Extract Wine Pricing Data Across Global Markets For Insights
Author: Den Rediant
9. Why A Tactical Picatinny Rail Forend Takes Your Remington 870 To The Next Level
Author: Slade Street Tactical
10. Powering Your Social Media Growth With Affordable Marketing Panels
Author: Smm Panel
11. Documenting Your Iso 50001 Procedures Effectively
Author: Sarah
12. Powering Progress With Quality Transformers– Kanyaka Parameshwari Engineering Pvt. Ltd
Author: Ojeshwani1
13. Cas No: 85118-00-9 Manufacturers
Author: vasista
14. How To Create Custom Clothing Online Without Compromising On Quality
Author: Guangzhou Beianji Clothing Co., Ltd
15. What Should You Know About Flat Roofing In Barrie?
Author: Ryan Seacrest