ALL >> Business >> View Article
Epoxy Zinc Rich Primer Coating
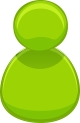
The primer is the most important layer of the coating as it acts as the base of the specified top coating required to prevent rust. It also provides the next layer to hold the surface, thus enabling the subsequent coating films to stick properly. Therefore, the primer contains the binders needed to stick to the substrate and form the next coating system layer.
Since the primer must cover the surface defects of the substrate, it must be carefully matched to the surface features such as porosity. If parts of the top coat are cracked or damaged, the Epoxy Zinc Rich Primer Coating in the primer will continue to provide corrosion protection for a limited period of time.
Epoxy Zinc Rich Primer Coating
What Are Zinc Rich Primers?
Epoxy Zinc Rich Primer Coating are used to protect steel surfaces from corrosion. The most effective means is to protect vital equipment from moisture, rust and rust.
Unlike regular paints or epoxy, which resist corrosion by creating an impenetrable barrier between the metal and atmospheric moisture, zinc-containing primers provide Protexion LLP through electrical media.
Epoxy ...
... Zinc Rich Primer Coating provide excellent corrosion resistance, especially in aggressive corrosive environments. Zinc-rich primers are for structural steel members, not for thin-gauge metal sheets, as you would find on your equipment.
There are two types of zinc-rich primers: organic zinc primer and inorganic zinc-rich primer.
Basics of Epoxy Zinc Rich Primers
Epoxy zinc-containing primers belong to the family of zinc-containing coatings that are applied to protect iron surfaces from corrosion. These primarily serve as single cathodic protection products. Since zinc is anodic to steel, these particles rust first, preventing the iron layer beneath the primer from rusting.
The zinc product is a zinc oxide powder that opens up the remaining zinc coating for further oxidation, providing a protective stabilizer. Therefore, zinc-based primers provide sacrificial cathodic protection for steel substrates.
Low Epoxy Zinc Rich Primer Coating contain approximately 55% zinc by weight, while zinc-rich epoxy primers contain approximately 80 to 85% zinc by weight.
Organic Versus Inorganic Zinc Rich Primers
Epoxy Zinc Rich Primer Coating is an organic coating and requires a top coating for durable and reliable heavy-duty protection. It can be applied with an airless spray, air spray, roller or brush - and the simplicity of use as well as the durability of the surface make it suitable for onsite maintenance applications. However, excessive use of primers containing organic zinc can cause cracks, which can lead to coating failure. Failures often appear on welds and corners.
On the other hand, primers containing inorganic zinc have the advantage of not requiring a top coating. In this case, silicate is usually used as a binder. This primer cannot be applied to the site, as it is very important to create the right surface by abrasive blasting of the surface.
There are four major differences between organic and inorganic zinc-rich primers:
Binder. Organic forms use epoxy, butyl, urethane or other organic resins, while inorganic zinc coatings generally use zinc silicate binders.
Display temperature. Inorganic zinc can work at high service temperatures, while organic or epoxy zinc is known to work at low temperatures.
Lifetime service. Inorganic zinc has a longer service life than organic zinc. In marine environments, for example, inorganic zinc can last up to 15 years - while organic zinc has a service life of 13.5 years.
Resistance to abrasion, sunlight and solvents. Inorganic zinc is also known to be more resistant to organic zinc.
Areas of Application
Zinc Rich Primer Coating are widely used to protect steel piping and structural members exposed to corrosive environments. These primers with advanced formulations are often designed for highly corrosive environments with high relative humidity, high alkalinity and marine and offshore properties such as coastal power projects, pools, oil refineries / platforms and aggressive environments facing mining machinery. It can also be used to repair damaged Epoxy Zinc Rich Primer Coating and galvanized ferrous surfaces.
More about information for Epoxy Zinc Rich Primer Coating then Visit our site -
http://www.protexion.in/zinc-rich-coating-and-paint.php
Add Comment
Business Articles
1. Remodeling Contractor Kitchen Secrets: Create A Space You’ll LoveAuthor: Scott
2. Lucintel Forecasts The Global Usb Wall Charger Market To Grow With A Cagr Of 6.2% From 2025 To 2031
Author: Lucintel LLC
3. Lucintel Forecasts The Global Tunnel Lighting Market To Grow With A Cagr Of 5.5% From 2025 To 2031
Author: Lucintel LLC
4. Lucintel Forecasts The Global Thyme Extract Market To Grow With A Cagr Of 6% From 2025 To 2031
Author: Lucintel LLC
5. Lucintel Forecasts The Global Tamper Evident Label Market To Grow With A Cagr Of 5.2% From 2025 To 2031
Author: Lucintel LLC
6. Lucintel Forecasts The Global Surface Cleaning Product Market To Grow With A Cagr Of 5.2% From 2025 To 2031
Author: Lucintel LLC
7. Why You Should Always Choose A Digital Business Card
Author: Angus Carruthers
8. The Virtual Receptionist Is An Asset For Your Business!
Author: Eliza Garran
9. Lucintel Forecasts The Global Supercritical Water Oxidation Technology Market To Grow With A Cagr Of 10.8% From 2025 To 2031
Author: Lucintel LLC
10. Strengthening The Future Of Production: The Role Of Manufacturing Supply Chain Solutions
Author: Trinity Diaz
11. Lucintel Forecasts The Global Sprocket Market To Grow With A Cagr Of 5.5% From 2025 To 2031
Author: Lucintel LLC
12. Price Benchmarking For D2c Brands With Ai Scraping | Actowiz Metrics
Author: Actowiz Metrics
13. What To Expect From The Inspection Company (tic)
Author: TIC
14. Budget-friendly Building Materials In Mumbai
Author: lTrikamdas
15. Digital Gold 2.0: The Case For Gold-pegged Crypto Stablecoins
Author: annagreyson