ALL >> Business >> View Article
What Is Steel Fabrication Profile Cutting?
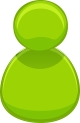
The term steel fabrication profile cutting is often used to refer to metal cutting carried out with the use of a plasma torch.
Plasma torches are commonly used in construction, shipbuilding, and aerospace industries. They can also be found in repair workshops for heavy equipment, motorcycles, agricultural tractors, and cars.
The main purpose of this type of cutting is to shape metal sheets.
The thickness and the type of metal greatly determine what kind of cutting process will be used in order to get the desired result.
Plasma cutting is only one out of several ways to cut steel sheets. The other options include oxyacetylene, laser, water jet, CNC plasma & laser cutting, shear & guillotine, etc.
When cutting sheet metal with high-speed plasma torches, the resulting cut is smooth and accurate. The material's edges are also shiny thanks to the ionization process. These characteristics make plasma cutting excellent for parts that need a sleek finish.
Plasma torch operation can be ...
... done in air or in a vacuum.
This cutting process has an advantage over oxyacetylene, laser, and water jet methods in that plasma cuts are more precise thanks to the short heat affect zone.
With these other cutting technologies, it is necessary for the metal sheet to be clamped on a fixed surface. This way it is possible to achieve perpendicularity between the plate's surface and the cutting head.
With plasma cutting, no clamping is needed since the sheet can be cut when held in the air or in a vacuum. This allows for better result accuracy when trying to perform very delicate work.
Plasma torches are composed of three components. One is an electric arc power supply that generates electricity to ionize the gas inside the torch. The other one is a high-velocity stream of ionizing gas flowing between the electrode and the metal sheet.
The third component is the torch head which consists of a constricting nozzle, electrode, and insulating material on top of it. This insulation layer prevents electrical discharge overspray as well as sparks from causing fires or damaging equipment in the workshop.
The frame is another element of the torch, protecting it from overheating and mechanical damage.
Benefits of Profile Cutting:
- Precision cutting
- Minimal material waste
- Short heat affect the zone
- Cuts through a wide range of metal types and thicknesses, including wrought iron, stainless steel, alloy steel, aluminum and galvanized sheet, brass & copper.
Plasma cutter machines that use compressed gas as the source of plasma are generally suitable for profile cutting applications.
Using compressed air instead of oxygen allows for cutting through thicker metal at faster speeds. Oxygen plasma torches require higher amperages resulting in reduced cutting speed for very thick materials.
Since the energy density is lower with compressed air, they are less effective when dealing with thinner sheets or plates made of more conductive materials like aluminum and copper.
The thickness of the sheet metal will also determine which type of plasma torch should be used in a particular case. For thin metals usually a light-duty torch is sufficient while stronger torches are more efficient on thicker materials.
In order to achieve quality results, it's necessary to have an appropriate power supply and high-quality consumables such as a nozzle and a shield.
Induction heat cutting is a plasma process that uses induction rather than argon gas to create plasma. This method doesn't use compressed air, which results in no flame whatsoever when cutting metal sheets.
This technology makes induction heating machines very useful for applications where fire hazards are an issue such as nuclear energy plants, oil rigs, or hospitals.
Induction heating plasma cutters use an electromagnetic current to generate the plasma arc, keeping the high-speed gas stream away from the material's surface.
This way it is possible to avoid charring and spattering that damages workpieces in oxyacetylene cutting processes.
In other words, we can say that profile cutting is a process that allows metal sheets or plates to be cut into the desired shape. The sheet is moved through the cutting path as it passes over a nozzle.
An electric current ionizes gas surrounding the nozzle which creates plasma. This plasma fluid cuts through the metal surface, producing a smooth edge along the top of the workpiece where it was cut.
Add Comment
Business Articles
1. Lucintel Forecasts The Global Wall-mounted Ac Ev Charger Market To Grow With A Cagr Of 22.4% From 2025 To 2031Author: Lucintel LLC
2. Technology Landscape, Trends And Opportunities In Global 3d Printing Photopolymer Market
Author: Lucintel LLC
3. Lucintel Forecasts The Global Smart Home Market To Reach $372 Billion By 2030
Author: Lucintel LLC
4. Second Marriage Matrimonial – Verified Matches & Free Registration
Author: Truelymarry
5. Core: Leading The Way In Managed It Services For Businesses Across London
Author: IT Management
6. The Role And Function Of A Collection Agency
Author: Bennett Carter
7. Understanding Debt Collection Agencies: What They Do And How They Affect Consumers
Author: Bennett Carter
8. How To Use An Smm Panel Effectively For Fast Social Media Growth
Author: Smm Panel
9. Essential Tips For Beginners And The Power Of Professional Editing
Author: Sam
10. How To Improve Field Staff Efficiency With Geolocation Tools
Author: TrackHr App
11. Building An Effective Energy Management System
Author: Jane
12. Internal Auditor Training: The Key To Effective Risk Management And Compliance
Author: Sqccertification
13. Why Accurate Accounting In Property Management Is The Key To Higher Roi
Author: Harsh Vardhan
14. Kaal Sarp Puja In Trimbakeshwar – Benefits, Process & Trusted Pandit Contact
Author: Pandit Milind Guruji
15. Data Entry Vs. Data Processing: What’s The Difference And Why It Matters
Author: Allianze BPO