ALL >> General >> View Article
Brief Explanation About Working Of Asphalt Batch Mix Plant And It's Components
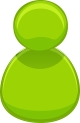
An asphalt mixing plant is a key piece of equipment for road construction companies. Each asphalt batch plant has many functions. They are more complicated than drum-type asphalt batch mix plant operations. This article will highlight the basics of Asphalt Batch mix plant! operations.
The four major functions that are required to operate any asphalt batching plant are:
Heating and drying the aggregates.
Weighing aggregates, bitumen, and binder materials.
Mix the bitumen, binder and aggregates.
Hot mix asphalt is discharged.
Types of asphalt plants
The mixing plants can be classified as drum mix or batch mix. Asphalt Batch plants: These plants make hot mix asphalt in batches. Drum mix asphalt plant: This type of plant produces hot mix asphalt in continuous production. These plants are often called counter flow and drum mix plants.
This is more than just a difference in production. Each equipment also produces different types of hot mix asphalt. This equipment can also be modified to produce hot mix asphalt from recycled material. There ...
... are variations for both drum and batch type plants that allow you to add RAP (Reclaimed asphalt pavement).
Manufacturer of Asphalt Batch mix plant!
These are the components of a standard asphalt batch-mix plant:
Cold aggregate feeder bins that measure and deliver the aggregate to the dryer drum
Conveyor that takes the cold aggregates from feeder and supplies them to dryer drum.
Heating aggregates in a drying drum using a burner
Elevator to feed hot aggregates to vibrating screen after drying.
Vibrating screens are used to separate hot aggregates into the appropriate compartments according to their sizes
Hot bins to store hot aggregates prior to weighing
Filler storage and weighing system
Bitumen storage and weighing system
Aggregate weighing system
Mixing unit for pug mills
Dry dust collector
Bag filter
Control system
Batching plants are named for their ability to make hot mix asphalt in large batches. The capacity of each batch will determine the size and shape of these plants. Because they can switch between different recipes, batching plants are highly in demand. Customers who require precise equipment that can switch between different recipes and works endlessly are best served by batching plants. This machine has a distinct advantage over traditional drum mixers.
Working of asphalt batch mix plant:
The asphalt batch plant's work includes heating and weighing aggregates, heating bitumen, filler material, and end mixing of aggregates, bitumen, and filler material in order to make hot mix asphalt. The mix material recipe in the control panel can affect the percentage of each item. You can also choose to alter the size or percentage of aggregates.
Reclaimed asphalt can be added to the hot mix plant's mixing unit. The RAP material must be proportioned before it is added to the mixing unit. Asphalt mixing plant manufacturers can provide either a stationary or mobile asphalt plant depending on your needs.
Asphalt Batch Plant suppliers!
Few operations are common to all asphalt batching plant operations:
Cold aggregate storage and feeding
Heating and drying aggregates.
Hot aggregates - Screening and storage
Heating and storage of bitumen, and filler material
Mixing bitumen, aggregate, and filler material
Final asphalt mix material to be loaded
A control panel allows for the management of all plant operations.
You can also add reclaimed asphalt to the mix.
For easy access, cold aggregates should be kept in stockpiles close to the plant site. These should be taken from storage or stockpiles and then fed into cold aggregate feeder bins. You should feed the aggregates according to their size. For eg. Separate bins are required for feeding aggregates of different sizes, such as 10 mm, 20mm and 40mm. These aggregates are then sent in controlled quantities to the drying unit. This can be done by a bucket elevator or conveyor. A drying drum is a rotating unit with a burner unit. This allows the heating of the aggregates. This aids in drying the aggregates. After the aggregates have been heated, they are transferred through a bucket elevator to a vibrating screening unit.
Depending on how many aggregates are used, there may be several decks to this screening unit. The screening unit can separate aggregates according to their size and store them in various compartments. Hot bins can be used to store the aggregates in storage before they are weighed. Bitumen is heated and filled into separate tanks. The pumping station is used to transfer bitumen from the weigh tanks. After the bitumen has been weighed, it must be pumped into a mixing unit to mix with aggregates. The filler material must be stored and weighed before being added to the mixing unit. The mixer is then used to mix the reclaimed asphalt payment material, bitumen, sized aggregates, and filler material. Mixing in the mixer takes a set time. Hot mix asphalt is produced. It is then loaded onto trucks and stored in silos until it is ready to be delivered to the paving sites.
Raw and unheated aggregates must be kept in separate bins according to their size. Individual cold feeder gates control aggregate flow.
Then, they are transferred via a belt or elevator to the drying drum.
The burner heats and dries the aggregates in the drying drum.
A primary dust collector is found in most hot mix plants. This unit collects heavy dust particles.
The dust collector is used in conjunction with a secondary polluting control unit, which is a bag filter. Plant with venture wet dust collectors may be available in certain cases.
The heated aggregates are transferred to the top by a bucket elevator. The screening unit is located at the top of the tower unit.
Multiple layers make up the screening unit. Aggregates pass the screening test. They are separated according to their size.
Each type of aggregate can be stored in separate hot bins. This temporary storage is used before aggregates can be weighed.
After being weighed, the aggregates are discharged to the mixing unit. They are then mixed with bitumen or filler material.
Bitumen is stored in bitumen tanks. Bitumen tanks heat bitumen to allow it to flow freely. Bitumen is pumped to the weighing bucket by a pump station. It is weighed in this bucket before being added to the mixer. The same principle applies to the filler material. The filler material is placed in a separate container before being added to the mixing unit.
After mixing the material, it is placed in waiting trucks or storage silos.
All operations are controlled by the control panel.
Cold feeding and storage of aggregate
Image:- Counter Flow Drum Mix plant Exporters - All Tech Group
Cold feed is the process of handling and storing aggregates in batch plants. It's similar to drum mixers. We often have different sizes of aggregates in different amounts in mix recipes. These can result in different hot mix asphalt recipes or proportions. The feeder stores the aggregates in various bins. Because the bins will be used, it is essential that they are full at all times. It is important that there is enough material available at all times. The material should flow continuously. You should also ensure that your bins are properly filled. Some bins will empty faster than others, and these bins should be filled again and again. Consider a mix that contains 20 mm more aggregates. This 20 mm aggregates will be used more quickly than the others. Some bins will overflow if they are not properly fed. Variations in the amount of aggregates in cold feed can lead to significant temperature changes in the aggregates as they leave the drying drum. The vibrating screen, bucket elevator, dryer and dryer will be overload by excessively feeding the aggregates. Variations in aggregate size can also impact the moisture content of the final hot mixture asphalt.
Cold feeding batch mix and aggregate storage
These issues contribute to the uneven quality of final asphalt, which can be a problem. Asphalt plant manufacturers should ensure that the feeder bins have empty bin indicators and moisture indicators. This will allow you to control the feeding process.
Controlling the amount of aggregates that leave the aggregate feeders is also important. This will reduce the rate of degradation. This is important because it can cause problems later on.
Heating and aggregate drying
Once the aggregates have been removed from the feeder units, they will be transferred to the dryer drum. The drum rotates, transferring the aggregates to one side. The aggregates are heated to the required temperature during this stage. The heat from the burner is transferred to the enclosed dryer chamber, which removes the moisture. The dryer must be controlled in terms of temperature. The temperature indicators play a crucial role. It is important to check the temperature on a regular basis. This is where moisture checks are crucial.
Operation Dryer
Asphalt mixing plant manufacturers make conventional dryers that are revolving drum drums. They are 5-10 feet in diameter, 20-40 feet long. A dryer's main component is the burner unit. It is crucial that the dryer drum be designed in synchronization with the burner. This will ensure the best heating and the lowest fuel consumption. The burner can burn diesel or any other liquid fuel. The burner can also burn natural gas and coal. Diesel burners use diesel and air to fuel their combustion. The blower fan blows the required air for combustion. There are different mechanisms for heating and lifting the aggregates.
Image:- Asphalt Batch Mix Plant Supplier - All Tech Group
Heating and aggregate drying
The dryer drum is inclined. Aggregates will enter the drum at the upper end and leave at the lower end. The time aggregates spend in the drum will depend on many factors, including the drum's slope, diameter, length, flight speed, and the drum's rotation speed. Higher chances of aggregates being heated the longer they spend inside. For best results, the drum must have a proper air-to-fuel ratio. The drum is pumped by the blower. It will also keep the burner flame away from the drum so that heat can be evenly distributed to the aggregates. This will give you the best results and the most efficient removal of water. The amount of oil required to burn fuel will decrease if the air volume is smaller. This can cause an oily coating to be left on the aggregates, which is bad for the final asphalt mixture.
The dryer drum is designed to work efficiently with aggregates up to 5% moisture content. Asphalt plant manufacturers typically design it to be efficient (without a drop in production). However, dryers are not necessarily ineffective for higher moisture aggregates. The dryer drum calculation is affected by a dryer drum's moisture content of 5%. The dryer drum will need to receive less aggregates if the aggregate moisture content exceeds 5%. This will result in a decrease in the drying drum's capacity, which can reduce the output of an asphalt mixer. The dryer drum's fuel consumption is a major concern for asphalt plant buyers. This is a costly operation that can make a huge difference. The drying drum's efficiency determines the equipment's capacity.
Hot aggregates - Screening and storage
The success of any asphalt mixer is determined by how well it screens. Because it allows you to separate the aggregates according to their sizes, screening is essential. After the aggregates have dried, they can be transferred to the multi-deck screening unit. This is done efficiently by an enclosed bucket elevator system. The screens have multiple layers that allow the aggregates to pass through. This will allow you to separate the aggregates into different fractions and place them in different hot bins. This unit is the topmost part of the tower unit for the batch mixer.
Screening unit
This set includes several screens that are different in size. They are arranged one above another. The scalping screen is at the top. It rejects any material that is too large. The screen is followed by the other screens below it. From top to bottom, the sieve sizes of screens decrease. For smaller particles to pass through, the largest sieve size will be found at the top screen. The screen for sand is located at the base. It will have the lowest clearance. Screens are used to separate aggregates into hot bins.
Image:- Batch Mix plant Manufacturer -All Tech Group
Because large quantities of aggregates are likely to pass through the screens, the area of screening should be large. The screens should be cleaned and maintained in good condition. The screen's handling capacity should be equal to the capacity of the dryer, feeding capacity, and pug mill capacities. Overfeeding too many aggregates will cause them to ride on the screen and spill out of the overflow section, resulting in energy wastage. The screens will become inefficient if they are damaged. Larger particles can get stuck in the screens, making it difficult for smaller aggregates to pass.
Hot Bins
The hot bins are located just below the screening unit. The size and capacity of hot bins will depend on how large the screens are and how big the plant is. The hot bins are used to store separated aggregates in different chambers according to their size. Hot bins must be large enough to store material of all sizes. The partitions must be free of holes and prevent mixing of different aggregates. Indicators that indicate when the hot bin is full are provided on hot bins.
Heating and storage of bitumen, and filler material
Asphalt batch plants need to have adequate storage of bitumen. It is essential that bitumen be kept at the plant in a consistent manner. Bitumen tanks can be used to heat and store bitumen, so it flows freely and stays liquid. To prevent heat loss, asphalt storage and supply tanks have full insulation. Bitumen can be heated directly or indirectly. Customers can request different capacities of bitumen tank. A suitable capacity pumping station will transport the bitumen to the weigh tank for weighing.
Bitumen tanks are used for the storage and delivery of asphalt
The mixing unit can also be used to mix filler material. The mixing unit can also be used to return the bag filter dust. A separate unit is available for filler material.
Mixing binder, aggregate, and other recycled materials
Because the aggregates are kept in separate containers, they can be weighed individually before being added to the pug mill mixer. Before bitumen can be added to the mix, it must be weighed separately. The same principle applies to the filler material. Once the bitumen has been weighed, it can be introduced into the pug mill unit to be weighed. Every day, it is crucial to inspect and verify the accuracy of binder weight buckets. The tare weight of a bucket can be affected by bitumen that has gotten stuck during the previous day's operations. This will reduce the amount of binder that is added to the pugmill unit.
It is possible to add recycled material. The material is then transferred to its weighing device and then into the pug mill's mixing unit.
Image"- Batch Mix plant manufacturer -All Tech Group
Mixing binder, aggregate and other recycled materials
The mixing zone in which aggregates, bitumen, and filler material are thoroughly mixed for a fixed time is called the pug mill mixer. Two horizontal shafts are connected to form the pug mill mixer. These shafts are equipped with tips and pedal arms. The shaft rotates and the tips rotate, resulting in homogeneous mix. This allows for high quality hot mix asphalt. When worn out, these tips and arms can be replaced. When the inner lining of a pug mill mixer becomes worn, it can also be replaced. The majority of asphalt batch plant manufacturers offer the pugmill mixers with hot oil jacketing to ensure that the unit is always hot.
Final asphalt mix material to be loaded
The last stage of operation for an asphalt batch mix plant involves the release of hot mix asphalt onto a waiting truck or into storage silos. Depending on the requirements of the customer, storage silos may be different in capacity. Many asphalt batch mixer manufacturers offer storage silos that can be insulated to maintain the temperature for long periods of time.
A control panel allows for the management of all plant operations.
A control panel allows for the control of all operations in the plant.
The control panel is the heartbeat of the unit and controls all aspects of the plant's operation from one place. The control panel allows for the addition or deletion of mix material recipes. The panel also shows all of the relevant parameters. Modern asphalt batch mixers have sophisticated controls that ensure smooth, error-free operation from one place. It is possible to view plant status and solve any errors. It is now possible to print batch reports directly from the control panel.
Add Comment
General Articles
1. How Solicitors In Craigavon Handle Property DisputesAuthor: Jph Law
2. Car Suspension Repair Dubai – Drive Smooth, Stay Safe
Author: James
3. Top Choice For Apple Ipad Repair Dubai – Fast, Reliable, And Affordable
Author: James
4. Best Fan Designs By Industry – Id And Fd Fans
Author: Neel Rao
5. Chand Par Shayari In Hindi
Author: Banjit
6. British And Irish Lions Face Fitness Fears Before Brisbane Test
Author: eticketing.co
7. What Are A4-70 Bolts And Why Are They Important?
Author: Dalloyed Fastners
8. Is Apache Superset Right For You? 5 Alternatives To Consider
Author: Vhelical
9. Redash Alternative For Data Visualization
Author: Vhelical
10. Nfl Games: Chiefs-chargers Clash Amid Cbs Uncertainty
Author: eticketing.co
11. Ai-powered Affiliate Funnels? Fusion Ai 2025 Review Exposes The Truth
Author: Joshua thomson
12. Looking For A Nursery In Rolla Sharjah? Visit Bumble Bee Nursery Today!
Author: sharjah
13. Platinum 1000 l Stainless Steel Tank For Ro Water Storage: Pure, Safe & Durable
Author: amalagrawal
14. Best Double Meaning Shayari With Images
Author: Banjit
15. The Highwaymen’s Journey Through Time: From Roadside Paintings To Museum Walls
Author: Highwaymen Art Specialists