ALL >> Food,-Cooking-and-Drink >> View Article
Chores Of Cip In Food Plant Hygiene
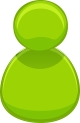
To provide standard and superiority food for consumers regularly, comprises of many practices from production, processing to packaging stages. In this practice, hygiene, a vital procedure has been implicated, which is necessary in the food processing circumstances for standard food. Hygiene can be abided either by cleaning, sterilizing, disinfecting, or placing in extreme temperatures. Still the complication is around whether choosing of manual or machine work for whole food plant hygiene.
Suppose maintaining cleanliness manually in high scale is a challenging process as well as impossible for dismantling and manually clean the piping and equipment. To begin with production, cleaning is the foremost step for preparing the processed line of products. Sequentially, it can be attained by CIP (clean in Place) unit has been efficient segment of any food processing plant.
What is CIP?
Cleaning in place, short as CIP is a set of procedures used to properly cleaning the processing equipment without removal of pipes or equipment in practice of food plant hygiene. In all facilities CIP requirements are unique. The ...
... elements, sequence, and duration of the process varies from system to system, but few common steps are incorporated in most cycles are enumerated below.
Common phases in CIP cycle
Pre-rinse – First step in the cycle that takes the responsibility for physically cleaning the equipment. Discards most remaining visible residues in production lines along with dissolves sugars and partially melts the fat.
Caustic wash – Soften fats. The alkali used in caustic washes has a high pH concentration of 0.5-2.0%. Most times water can be saved by, the caustic wash can be returned to its tank and reused multiple times.
Intermediate rinse – In case the traces of remaining caustic are available, that can be flushed from the system by fresh water or rinse recovery tank.
Final rinse – Flushes out residual cleaning agents. Some cases water saving is applied by final rinse can be recovered and re-used as pre-rinse solution for the next cleaning cycle.
Sanitizing rinse – Assist in killing the microorganisms before next production run. Major task is of picking the suitable disinfection for destroying or sterilizing the fungi or bacteria.
Since every cycle has unique parameters, some facilities choose to do some or all of these optional steps
Food manufacturing plant facilities The construction of food manufacturing and processing equipment must be carried out in accordance with the regulations of the relevant food regulatory agency. Toilets should be equipped with automatic closing doors. Foot or knee taps should be installed on hand washing stations with water supply temperatures of 43°C and 50°C. Soap bars increase the spread of microorganisms, so it is recommended to use a liquid soap dispenser. In order to dry your hands, it is recommended to discard sanitary napkins.
Control of microbial infection in beverages
It is essential to sanitize and clean the brewery equipment that process the wort because beer self-sterilize itself in 5-7 days and in freshly cooled wort, undesirable bacteria and viruses grows rapidly. Developing and maintaining a comprehensive sanitation program can be an effective mean to prevent contamination and infection in the beverage products. Ultraviolet (UV) light can be effectively used to control microorganisms and to eliminate airborne microbes. UV light is nonionizing and non-residual disinfectant therefore can also be installed in water treatment to obtain residue-free water.
Hygiene practices in beverage industry
HACCP (Hazard Analysis and Critical Control Point) program should be implemented which ensures microbial and chemical monitoring to assure safe production of food products. System such as conveyor lubricant system can be installed to reduce microbial load. Interior and exterior of the beverage equipments, conveyors and fillers should be sanitized and cleaned on a regular interval. Walls and floors should also be foamed or gelled on daily basis.
Track FMT magazine https://fmtmagazine.in/food-plant-hygiene/ for more engaging info of food plant hygiene
Add Comment
Food, Cooking and Drink Articles
1. How To Dial-in Any EspressoAuthor: Madhu
2. How To Pick The Perfect Mithai For Every Indian Festival
Author: Delicacy
3. How To Prepare Chinese Chicken Stock?
Author: Coba Grill HK
4. Why Soaked Dry Fruits Are A Must-have In Summer
Author: Julie R. Thompson
5. Maximize Hygiene And Portability With Small Paper Containers For Snacks And Dips
Author: Gujarat Shopee
6. The Importance Of The Amazing Good Quality Canned Tomatoes
Author: Tianjin Shinhoo Food co.,ltd
7. How To Prepare Chinese Sliced Tofu Salad (凉拌豆腐丝)?
Author: Coba Grill HK
8. Unleashing The Magic Of Everyday Meals With Innovative Kitchen Tools
Author: Sundar
9. What Food Safety Experts Think About Reusable Paper Containers For Leftovers
Author: Gujarat Shopee
10. The Complete Guide To Materials Used In Custom Cheese Paper
Author: Custom Butcher
11. Hyderabad Catering Service In Hyderabad: Perfect Blend Of Taste And Tradition
Author: gkbcatering
12. Top-quality Hyderabad Catering Services For Every Occasion
Author: gkbcatering
13. Where To Buy Premium Tea Online: A Guide For Discerning Tea Lovers
Author: John Smith
14. The Comforting Simplicity Of Miso Soup: A Nourishing Everyday Favourite
Author: John Smith
15. Caterers For Corporate Offices In Hyderabad
Author: SREEFOOD