ALL >> Business >> View Article
Importance Of Hygienic Design Of Food Processing Industry Equipment
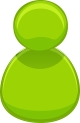
Food processing firms are aware of the importance of food safety as it significantly enhances consumer confidence. Hygienic design encompasses the machinery and overall infrastructure required in the food processed for consumption.
This is one of the most prioritized aspects in the food processing industry. Contamination of food has a direct impact on the health and lifestyle of the consumers. The equipment, therefore, should be designed accordingly.
The prime principles of the design of hygienic food equipment:
• Establishing standards, that all the workers will be adhering to
• Sealing hollow area and crevices in the equipment
• Preventing condensation build-up on machinery
• Getting access to all the areas of equipment in the plant for cleaning
• Integrating materials that are compatible throughout a factory
• Ensuring easy microbiological cleaning
• Separating MS & SS tools.
In the manufacture of food processing equipment the importance of hygienic design cannot be over emphasized.
Need For Hygienic Design
Manufacturers dealing ...
... with food equipment seek ways to help their customers keep the machinery free from contamination. Manufacturers must design the machines accordingly, removing the risks related to microbiological organisms or toxins contaminating the food products. However, food processing firms should know, that equipment with hygienic designs can be cost efficient. Due to the choice of better-quality materials, the upfront cost may be higher. However, in the long-term, the operational costs are low.
Currently, the public is aware of food safety, and therefore, food processing firms are focusing more on hygienic designs. In the digitized world, communication through social media takes place much faster, as compared to the traditional forms. A damage to reputation can be a big threat to business. Therefore, food retailers and food processing plants look out for equipment designed to minimize the chances of contamination. As manufacturer we should address these concerns and construct equipment, that fulfills the evolving demands of the customers.
What Are The General Design Principles For Food Processing Equipment?
The primary concern about safety in food processing equipment revolves around the surfaces that come in direct contact with the food. Therefore, the surfaces can be classified into two categories:
• Contact surfaces
• Non-contact surfaces
Contact Surfaces
The equipment surfaces, that have a direct contact with food products should meet the following requirements:
• The surfaces need to be impervious and smooth
• They should not have any type of crevice or crack
• Be non-conductive to contamination
• Made from materials that are nonabsorbent and nonporous
• Be non-reactive to food products
• Be easily cleanable
• The surfaces do not have any toxin
• Be durable
• Require little or no maintenance
• Be resistant to corrosion
The surfaces of equipment that remain covered in any type of non-metallic or alloy material must adhere to these standards. Regardless of the conditions in the factory environment, the surface should not have any kind of chipping, bubbling or flaking. During fabrication, the modifications like soldering and welding need to be done using the right materials. This ensures that the surface meets the required design principles while maintaining hygiene.
Considering the importance of hygienic design of equipment used in food processing industry, it is important to use the right materials and design techniques. The designer, firstly, should determine the requirements, that can keep the equipment from causing contamination. Besides, the manufacturers and food processing firms should make a commitment to cleanliness and hygienic design in the interest of customer health and safety. This ensures business viability and increase in reputation of the firms as they match the expectations of their consumers.
Reitz India Industrial Centrifugal fans are custom designed to serve the needs of various processes in industries like cement, iron & steel, power plants, fertilizers/ chemicals and more. As a top quality ID Fan manufacturers , Reitz India has set a benchmark in delivering superior fans with high quality features and better industrial standards.
Add Comment
Business Articles
1. Boosting Industrial Strength With Premium Flanges Manufacturer In IndiaAuthor: Metalica Forging Inc
2. The Evolution Of Fasteners: From Basic Joints To Advanced Applications - Caliber Enterprise
Author: caliber enterprises
3. China Business Email List – Unlock Targeted B2b Leads Across China With Ready Mailing Team
Author: Istiya isti
4. Types Of Lotion Dispenser Pumps: A Complete Guide
Author: Trisha Menon
5. What Are Aluminum Honeycomb Panels?
Author: Trisha Menon
6. 5 Indian Brands Winning With Pwas (and What You Can Learn From Them)
Author: Shubham
7. Djp Right Fit Recruiting Owner, Debra Parent, Voted In As A Member Of The Naer
Author: Steven Dubin
8. Berger Cpafirst: Your Trusted Accounting Partner In New Jersey And Nyc
Author: bergerCPAFirst
9. Get An Affordable Plumbing Repair Company Near You In Bangalore
Author: Smita Jain
10. Your Trusted Source For Real-time Number Game Results
Author: Manish
11. Pourquoi Certaines Cartouches Ruinent Vos Impressions ? Voici La Vérité
Author: john
12. Choosing The Correct Tackle Enhances The Smoothness And Satisfaction Derived From Nicotine Mariners
Author: vapewholesalepoint
13. Stundenrechner Benutzen Vorteile Und Tipps
Author: Steffen Stahl
14. Boost Your Online Business With Expert Marketing Help
Author: Usama Sakhawat Bajwa
15. Aghni Gold – The Smartest Place To Sell Old Gold For Instant Cash
Author: Aghnigold