ALL >> Others >> View Article
Concrete Core Drilling & Inverted Drilling: Everything You Need To Know
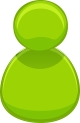
During your mining or construction endeavor, you will inevitably need to cut through concrete. However, cutting concrete is a difficult operation that requires specialised equipment and methods. This is where core drilling and inverted drilling come into play.
You may question the necessity of concrete core drilling for your undertaking. What is upside-down drilling? What equipment is utilised for core drilling? How are core drilling and inverted drilling applicable to the construction industry?
Fortunately, we will cover everything you need to know about concrete core drilling and inverted drilling, from how they operate to their benefits to concrete core drilling techniques. After reading this article, you will have a better understanding of the subject matter and why core drilling may be required for your endeavour.
What Is Core Drilling for Concrete?
The process of concrete core drilling entails cutting precise cylindrical holes in concrete walls, floors, and ceilings. This procedure is essential in construction for creating ...
... openings for, among other things, electrical, plumbing, and HVAC systems. In addition, core drilling is utilised to create anchoring holes for bolts and dowels in concrete surfaces.
Drilling a core requires a specialised machine with diamond drill blades. The diamond drill bits are utilised for core drilling because they can effortlessly pierce through the surface of the hardened concrete with minimal effort and maximum precision.
A benefit of core drilling is that it produces less commotion and less dust and debris. This makes it appropriate for noise-sensitive environments such as schools, hospitals, and healthcare facilities.
What machine is utilised for core drilling?
For concrete core drilling, various devices are available, including handheld core drills, stand-mounted core drills, and rig-mounted core drills. However, diamond concrete core drills are currently the most popular.
Diamond concrete core drills are outfitted with diamond drill bits that are composed of a steel tube coated with diamond crystals at the drilling end. The diamond-tipped bit is designed to remove material as it rotates, resulting in a cavity that is clean and precise.
How do diamond drills operate? The drill bit rotates at a high rate, and the operator applies gentle force to the machine in order to drive the bit into the concrete. In order to prevent overheating, it is also lubricated with water or specialised cooling substances. The hollow centre of the drill enables a solid cylinder of the rock, concrete, or other material being drilled to move up through the drill bit and out the open end.
Diamond core drill bits are significantly more effective than conventional core drilling equipment due to their increased precision, reduced mess, and low levels of heat, commotion, and vibrations. Important in the construction industry to prevent surface flaking and rework.
In addition to concrete, core drills can cut through granite, porcelain tile, fiberglass, limestone, and even ice.
What Applications Does Core Drilling Serve?
There are numerous applications for core drilling in the construction and industrial sectors. It is frequently employed to create apertures for new electrical conduits and cables, plumbing pipes, and concrete reinforcement. (starter bars).
In general, core drilling is required for the following applications to generate openings in existing concrete or brick structures:
Systems for plumbing and electricity.
Organizing cables.
HVAC Ductwork.
Ventilation Wells.
Actual Sampling.
The use of anchor fasteners.
Demolition.
Restoration.
Ballard structure
What Does Inverted Drilling Entail?
Inverted drilling is, as the term suggests, core drilling performed in an upward orientation. Instead of drilling from the top down, as with conventional core drilling, the drill bit is inserted into a surface cavity and then drilled upward. This method is typically employed when there is no direct access from above the structure or when the concrete's surface cannot be marred. For instance, inverted drilling may be used when installing pipelines or cables in a parking garage, where drilling from above could cause surface damage or impede traffic flow.
In commercial and industrial contexts, inverted drilling is commonly used to create openings for lighting fixtures, ventilation systems, and fire sprinklers. Drilling inverted is more difficult than conventional core drilling because the operator must work in an inverted position, which can be physically demanding.
When is the Need for Inverted Drilling?
In situations where access from above is restricted, such as on ceilings, walls, bridges, tunnels, and road surfaces, construction workers and contractors frequently use inverted drilling to create apertures for the following:
Cables
circuitry and circuitry
Lighting devices
HVAC systems
Ventilation systems
Plumbing piping and fire apparatus
Techniques for Drilling Concrete Cores
In the construction industry, there are two primary concrete core drilling techniques: moist core drilling and dry core drilling.
Hydraulic Core Drilling
Wet core drilling is the most prevalent technique in the construction industry due to its ability to propel the drill bit through concrete structures more quickly and efficiently than traditional core bits. During the drilling procedure, water is used to cool the drill bit and flush away debris. The water lubricates the cutting surface and prevents overheating of the drill blade. Wet core drilling is prefered for drilling holes with larger diameters and is best adapted for use on horizontal surfaces like floors, pavements, and bridges.
Among the benefits of moist core drilling are:
The water serves to suppress dust and debris, making the workplace safer and cleaner.
The drill bit is cooled by the water, which reduces the danger of overheating and wear, thereby extending its lifespan.
The water lubricates the tool, allowing for more precise and efficient drilling.
Drilling with a wet core is appropriate for a variety of materials, including concrete, asphalt, stone, and masonry.
These are some of its disadvantages:
Wet core drilling necessitates additional equipment, such as a water supply and a wastewater disposal system, which can increase the project's preparation time and expense.
The need for a water source can restrict the drill rig's mobility, rendering it unsuitable for some projects.
The water can produce a slippery, wet surface, increasing the likelihood of slip-and-fall accidents.
Dry Core Boring
Dry core drilling, as its name suggests, does not involve the use of water during the drilling procedure. Instead, air is used to cool the drill bit, and a vacuum system is attached to the drill rig to capture dust and debris.
Among the benefits of dry core drilling are:
Dry core drilling does not require a water source, making it more mobile and suitable for projects where water is not readily accessible.
It requires less equipment and water supply, which reduces project preparation time and costs.
Drilling with a dry core generates less mess and waste than drilling with a wet core.
Some drawbacks of dry core drilling include:
Dry core drilling generates more dust and debris than wet core drilling, which can be hazardous to workers and bystanders if the appropriate safety measures are not taken.
This can extend the duration of the undertaking, thereby increasing expenses.
Dry core drilling generates more heat during the drilling process, which can result in overheating or injury to the drill bit if it is not periodically cooled.
Dry core drilling generates more heat, which can increase the bit's wear and tear and shorten its lifecycle.
You should now have a clearer understanding of what core and inverted drilling is, the various core drilling techniques, their advantages and disadvantages, and how to choose the appropriate technique for your project after reading this article.
Add Comment
Others Articles
1. Choose A Color Before Investing In 1bhk Flat In Uttam NagarAuthor: Sanvi Real Estate
2. Quick Guide To Help Plan For Your Wedding Flowers
Author: Shishu
3. Reinvent Your Living Space With Smart Storage And Modern Sliding Wardrobes
Author: Madhu
4. Strategies To Mitigate Cognitive Biases
Author: ImPerfect
5. Sitecore Cms Development & Training: Everything You Need From Cli To Cloud
Author: Sitecore CMS Development & Training: Everything Yo
6. Learning From Bias – Real Stories And Smarter Strategies
Author: ImPerfect
7. The Best And Amazing Shipping Lawyers In China
Author: Shanghai Ganus Law Firm
8. Nickel Strip Lithium Battery
Author: Amit shah
9. From Wings To Wrenches: Can India Build Its Own Jet-set Future Before The World Closes Its Doors?
Author: kyone
10. Understanding Eating Disorder: A Path Towards Awareness And Healing
Author: ImPerfect
11. Elevate Your Kitchen With Durable Stainless Steel Benchtops In Auckland
Author: Kiwi Stainless
12. Digital Marketers In Travel Are Hitting A Career Wall Despite Industry Growth, New Update Why They’re Falling Behind In The Age Of Ai And Strategic Di
Author: PAWAN
13. How To Choose The Best Moving Company In 2025
Author: At AM Moving Company, we are movers Dallas, TX tru
14. Comprehensive Rodent Control In Springfield, Mo – Trusted Experts At 417 Pest Solutions
Author: 417 Pest Solutions
15. The Power Of Astro-numerology
Author: Reeth U Sarvvah